设计分析软件应该易于使用,同时应该允许用户介入。集成设计分析软件应该为用户提供控制网格化、单元 类型和顺序、理想化方案和所需求解方法的功能。 产品开发过程瓶颈 - 原型机开发及测试 新产品投入生产之前,需要进行原型机测试,以确保产品的性能符合客户的要求。某些测试只需要简单的物理样机,而其它测试(例如结构完整性测试)可能需要功能齐全的物理原型机。功能齐全的原型机比较昂贵,需要较长的制造时间,并会延长产品开发周期。尤其在需要许多原型机时更是如此。原型机测试通常会发现一些设计上的问题,这就要求重新制造原型机并进行测试以检查修改后的设计。通常,在产品设计最终定型之前,需要经历数次 成本高昂的设计-原型机迭代。 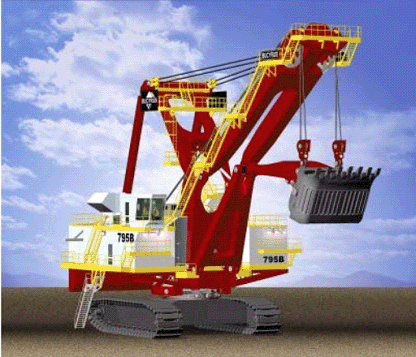
图片1 由Bucyrus International, Inc.提供 随着二十世纪九十年代信息技术的高速发展,产品开发过程从原型机制造-测试过程发展成为一种全新的产 品开发方法,即借助计算机辅助设计(CAD) 技术来开发产品。工程师开始使用有限单元方法(通常称为有限单元分析(FEA))来分析目标设计的计算机模型,从而节省了制造和测试原型机所需的费用和时间。利用FEA,工程师可以在各种强度下仿真设计模型的反应,并使用这些结果来改进设计性能,最大程度地减少对物理原型机的需求。 什么是设计分析? 用最简单的话来说,设计分析是一种用于在计算机上模拟物理行为的强大的软件技术。它会坏吗?它会变形吗?它会不会变得过热?对于这些类型的问题,设计分析能够给出明确的答案。工程师不需要制造原型机并精心制订测试计划来分析产品的物理行为,只需在计算机上快速而精确地获得这些信息。由于设计分析可以最大限度地减少甚至避免对物理原型机和测试的需要,因此,在过去的十年中,这种技术已成为主流技术,在制造业作为一种重要的产品开发工具使用,并且几乎应用于所有工程领域。 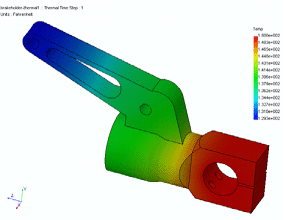
在图2中,红色区域表示潜在的故障 机械工程领域最常用的设计分析应用程序是应力分析。工程师通过对某个零件的应力(包括结构应力和热应力)进行研究,确定它是否会出现故障以及是否需要对设计进行修改以避免这些潜在问题的发生。设计分析还用于确定零件变形的可能性、零件和装配体的共振频率和振动模式、动力特性和地震反应、接触应力、温度分布等等。同时,设计分析还可用于分析流体:流体在管道中是气体还是液体、引擎进气管的空气和燃料的混合情况,以及熔融塑料在模具中的填充情况。设计分析真正的作用在于能够在不制造任何物件的情况下精确地执行这些类型的研究中的任一种。所需的只是一个由计算机辅助设计软件(CAD)产生的数字模型。
设计分析一体化 早期的设计分析软件包是相互独立且专业程度非常高的应用程序,与计算机辅助设计软件并不相连。自二十世纪九十年代中期起,随着以下重大技术的发展,行业主流开始从物理原型机转变为三维设计分析: - 三维实体建模软件变得更强大、价格更低廉、更易于使用; - 设计分析软件更强大、价格更低廉,更易于非专业人士使用; - Microsoft? Windows? 操作系统使用户在PC上使用CAD和分析应用程序成为可能; - 计算机硬件性能更加强大、稳定,价格更低廉。 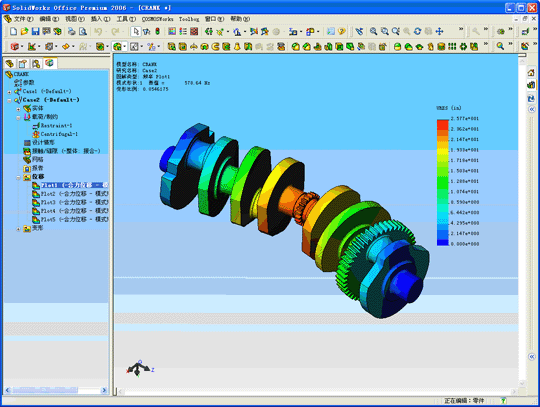
图3 CAD 和分析集成在一个窗口中 今天,台式机达到了二十世纪八十年代大型机的计算能力,价格却只是大型机的零头。高级设计分析工具的发展,使得制造商可以充分利用价格适中的计算能力以及主流设计分析的优势。强大的组合利用3D 实体建模和设计分析软件结合所产生的强大功能,工程师现在可以在计算机中测试设计,而不需要对设计进行原型机-测试迭代。 CAD 模型变成了虚拟的原型机,并且分析设计已经替代了物理测试,实现了更快、成本更低廉、效果更佳的产品开发。这样,产品更具创新性,更可靠,更适合市场需要。 不再只是专家的任务 |