张 轲1, 吕学勤1, 吴毅雄1, 2 , 张 悦1 (1. 上海交通大学, 上海 200030; 2. 金属基国家重点实验室, 上海 200030)
摘 要: 研制的自寻迹舰船甲板焊接移动机器人系统采用磁性轮式移动机构,外加十字调节滑块,利用激光PSD位移传感器外加扫描装置实时获取焊缝的二维偏差信息,选用数字信号处理器(DSP)作为系统的核心控制器件。伺服驱动采用集成的运动控制器和驱动器,实现了空间多自由度的协调动作。焊接时,在一定的误差范围内让机器人粗略跟踪焊缝,而由十字滑块实现焊缝实时的、精确的跟踪。该系统还具有自寻迹功能,即在焊前根据焊缝的特征信息自动寻找焊缝并调整自己的位姿到设定的待焊状态,由机器人自主地实现焊接对中和焊接起始点辨识。 关键词: 移动焊接机器人; 自寻迹; 焊缝跟踪; 舰船甲板
0 序 言 移动焊接机器人由于其移动性、强的磁吸附力以及较高的智能,已成为解决大型焊接结构件自动化焊接的有效方法,如大型舰船舱体、甲板、船身的焊接、大型球罐(储罐)的焊接以及大型石油输送管道的野外对接作业等等。有关这方面的研究已逐渐引起广大焊接工作者的关注,并有一些产品已应用于实际焊接工程。 但目前一般的移动焊接机器人只具有焊缝跟踪功能,焊前必须通过人为的方式将机器人本体、焊炬以及摆动机构调节到合适的位姿,还不具备焊前的自寻迹功能。如果焊前只需将机器人放在距焊缝一定距离的位置,而由机器人根据焊缝的特征信息自动寻找焊缝并调整自己的位姿到设定的待焊状态,即由机器人自主的实现焊接对中和起始点辨识,那么这对于大型结构件的高效自动化焊接无疑是非常具有实际意义的。 文中针对大型舰船甲板的全自动化焊接而研制的自寻迹式移动焊接机器人,它不但能实现横向大范围的焊缝实时跟踪,而且在焊前能自动寻找焊缝并调整自己的位姿到设定的待焊状态,即具有自寻迹功能。相对于其他的移动焊接机器人来说,系统具有更高的自主性。
1 系统组成 自寻迹式移动焊接机器人由磁性轮式移动机器人本体、焊炬位置调节机构、传感器及其扫描机构以及基于DSP的全数字控制系统等组成。系统整体结构如图1所示。
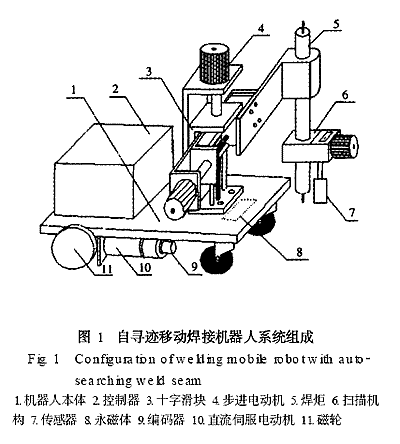
1.1 行走机构 轮式移动机构,行走速度快,转弯灵活,便于横向大范围的焊缝跟踪和焊前自寻迹工作,适合舰船甲板的自动化焊接。利用柔性磁轮作驱动轮并在车体底部安装强磁使小车有足够的磁吸附力,一方面防止了车轮打滑,增加了车体的稳定性,另一方面使小车能在具有一定坡度的工件上爬行焊接。驱动轮由两个直流伺服电机分别驱动并加光电编码器实时反馈以进行闭环控制,利用两驱动轮的差速实现小车的轨迹运动,如前进、后退、转弯等运动。小车最大行走速度为1.2m/min。 1.2 二维实时跟踪机构 在焊接中,要求移动焊接机器人的焊炬必须精确地沿焊缝以恒定的焊接速度焊接,而轮式移动机器人本体难以实现实时、准确的运动轨迹控制。为此,在移动机器人本体上增加了一个十字滑块调节机构,焊炬和传感器与十字滑块固连。十字滑块分别由两个四相步进电机控制,步进电机通过丝杆带动十字滑块移动,实现焊缝的二维跟踪,位移调节精度可达3.75μm/step。在焊接过程中,让机器人在一定的误差范围内粗略跟踪焊缝,而由十字滑块实现焊缝的精确的、实时的跟踪。在跟踪过程中,焊炬高度方向上的跟踪精度设定为±1.0 mm,而左右方向上的跟踪精度设定为±0.5 mm。 1.3 基于DSP 的控制系统 采用Ti公司F240系列数字信号处理器(DSP)TMS320F240作为控制系统的核心,外围电路主要由底层逻辑控制电路,传感器信号调理电路,以及伺服驱动电路和人机接口电路等组成,实现了空间多个自由度的全数字化控制,整个控制系统电路结构简洁,可靠,功能强大。而DSP和FPGA的在系统编程(ISP)特点,可以根据实时控制的需要,灵活更改电机驱动控制算法及电路的控制逻辑,使系统具有很大的灵活性和开放性。
2 跟踪传感系统 2.1 传感系统组成 传感器采用基于三角测量法原理的激光- PSD型位移传感器。它是利用不同高度位置的反射光在位置敏感检测器(PSD)上成像的位置不同,通过成像位置的不同,就可测得工件上不同位置距传感器的距离。将该位移传感器增加一旋转扫描机构,在焊接过程中,通过实时扫描焊缝坡口的横截面,就可以获得焊缝的二维偏差信息。扫描机构由一个四相步进电机控制,为实现对扫描角度的精细控制,步进电机采用细分驱动技术驱动,使电机分辨率达到400步/ r,在传感器的末端,位移精度可达0.01mm/step,完全满足焊接实际工程的需要。 2.2 信号处理及控制 传感器的信号处理及控制如图2所示。焊接过程中,位移传感器在旋转扫描机构的带动下实时扫描坡口横截面, PSD检测出扫描电机在每个扫描角度θ时所对应的位移量r,再经过坐标变换、数据处理后就可得到焊缝坡口的二维偏差信息。将此偏差信息送入焊缝跟踪控制器,控制器根据一定的控制策略,驱动十字滑块对焊炬进行高低、左右方向上的偏差调节。如果横向偏差较大,这个时候还需要同时对移动焊接机器人本体的位姿进行调节,使偏差始终控制在一定范围以内。
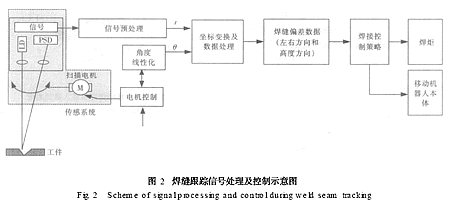 而十字滑块的横向调节机构在机器人运动时增加了焊炬自由度的冗余,使得跟踪控制变得复杂。此外,利用扫描坡口横截面可以获得横向扫描宽度以及坡口宽度、高度等的功能,可以用来进行焊前的自寻迹工作。
3 自寻迹算法实现 3.1 自寻迹过程 所谓自寻迹就是在焊前根据焊缝的特征信息自动寻找焊缝并调整自己的位姿到设定的待焊状态。也就是说,自寻迹不仅仅指自动寻找和识别焊接坡口,还包括对焊接起始点的辨识,它的最终目的是使小车车体与焊缝平行且焊炬位于焊缝坡口的中心,且焊炬位于焊接起始点处。当位姿调整结束以后,小车前进或者后退,传感器实时采集坡口断面的轮廓信息并与起始点的特征模型相匹配。当匹配成功,则表明系统成功寻找到焊接起始点,自寻迹过程完成,系统进入设定的待焊状态。系统约定小车在自寻迹前处于与坡口不大于90°的任意一角度。整个自寻迹过程如图3所示,其中O点表示焊炬和传感器所在的位置。E点表示位姿调整结束后小车前进或后退进行焊接起始点的辨识。
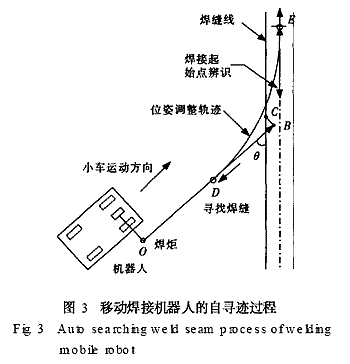 3.2 算法实现 由自寻迹过程可知,自寻迹算法主要包括坡口识别、切入角计算、轨迹规划、目标轨迹生成以及位姿调整以及起始点辨识等几部分。除位姿调整模块由控制系统的运动控制器实现以外,其余的几个算法模块均由Ti公司的数字信号处理(DSP) 芯片TMS320F240 (简称F240)构成的主控制器来实现。 对运动轨迹采用“时序控制”的方式实现,即根据运动参数及小车的切入角进行轨迹规划以后,通过机器人逆向运动学算法求出在每个对应时刻左右轮的角速度以及位置参数(即目标轨迹生成) ,然后通过后面的运动控制器进行位姿调整,就可以实现移动机器人焊接坡口的自寻迹,调整机器人的位姿到设定的待焊状态。而对于主控制器送来的位置指令或速度指令,则由底层的运动控制器来实现。
4 基于DSP的控制系统 4.1 系统硬件结构 在焊接过程开始前,要自动寻找焊缝并对调整轨迹进行运动规划,而在焊缝跟踪过程中,不但需要实时调整焊炬的位姿,同时还需要调整小车本体的位姿,显然系统是一个复杂的实时多任务控制系统。系统选用F240作为整个控制系统的核心,它运行速度快,有强大的运算功能和丰富的外围资源,另外集成了专为电机控制的脉宽调制(PWM)口和可以直接处理光电编码器反馈信号的捕获口,可以大大简化电路设计,提高系统的可靠性。另外, DSP强大的数字信号处理能力和运算能力,也便于运用各种先进的控制算法如神经网络、模糊控制等智能控制算法在系统上的实现,大大提高了系统的智能化程度。整个控制系统结构如图4所示。 F240作为整个控制系统的核心,负责在自寻迹过程中以及焊缝跟踪过程中所有信息的处理与运算,同时根据处理的结果控制十字滑块、移动机器人本体以及扫描机构的运动,同时也对焊缝跟踪过程中的故障进行处理等。 FPGA (可编程逻辑阵列) ,选用Altera 公司的EPM7128SLC84,负责综合所有的底层控制逻辑以及时序的处理,大大简化了外围电路设计,提高了系统的可靠性。利用FPGA具有在系统编程(ISP)的特点,可以方便的对系统进行在线升级,在线修改,大大提高了系统的灵活性、可重用性和可扩展性。 在系统运行过程中,良好的人机交互是非常重要的。DSP的长处在于其强大的数字信号处理能力,而MCU(嵌入式微控制器)的控制能力较强。所以系统选用MCU芯片-AT89C52作控制盒的CPU,主要负责各种参数的设定以及焊接过程中各种实时状态信息的显示等,比如焊接速度,小车的行走方式- 直线运动或者转弯运动,焊缝跟踪的控制模式-PID(比例积分与微分)控制或模糊控制或者是二者的混合控制,以及焊接过程的时序控制-通气/断气,起焊/停焊等等。如果与具有串口通讯的焊接电源联网,那么焊接规范参数也可以通过该人机接口进行设定。焊接过程实际上是一个强电磁干扰源,为保证通讯质量,系统采用RS-485接口方式进行通讯,并对传输信号进行屏蔽与隔离,大大降低了系统对噪声的敏感度。
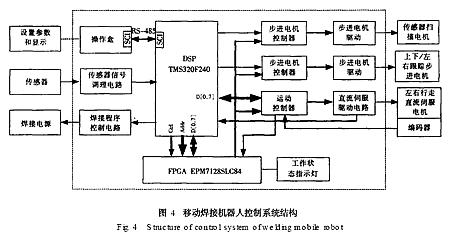 为了提高控制系统的可靠性,减少软件工作量,提高系统的响应速度,伺服驱动部分采用了专门的运动控制和驱动芯片。此外,在进行系统设计时,所有的输入和输出信号都进行了光电隔离,以提高系统的抗干扰能力,保证系统的安全、稳定的运行。 4.2 电机驱动控制算法 机器人本体的伺服控制采用位置环、速度环和电流环三环控制。位置环采用模糊PID控制,速度环采用PI(比例积分)调节算法,PWM实际上是一个比例环节,电流负反馈的引入在于调节电流回路的电流,抑制电流波动,并在电枢电流超过设定值时抑制PWM输出以保护电机。这使系统具有较好的动态和静态特性,既可以保证系统具有一定的抗干扰
|