图12 动轴瓦载荷工况下轴瓦孔在Y向变形 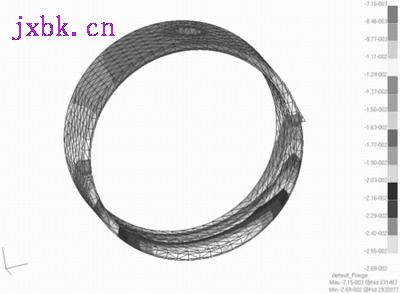
图13 动轴瓦载荷工况下轴瓦孔在Z向变形 轴瓦孔的变形会影响到最小油膜厚度,因此对它的变形估算很重要。对螺栓装配载荷工况引起的变形可以不予考虑,因为在装配螺栓后要对轴瓦孔进行机加工,变形被排除。对轴瓦进行装配引起的变形在各方向基本均匀,因此不作重点考虑。对动轴瓦载荷工况引起的变形,轴瓦孔在Y向的变形是3.47μm,在Z向是25.5μm,轴承间隙是40μm,变形远小于间隙,可以保证最小油膜厚度,如下文中图17、图18所示。 2.应力结果 如图14~图16所示,为螺栓预紧力等于45.5KN时框架和缸体的应力(Von Mises stress)分布。 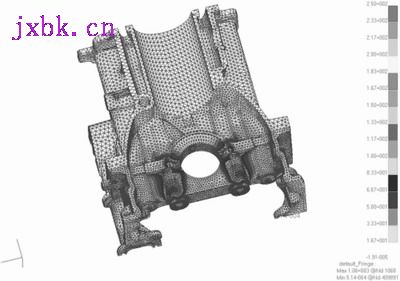
图14 框架和缸体的整体应力分布 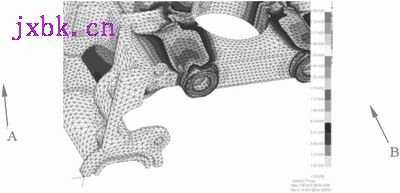
图15 框架局部应力分布 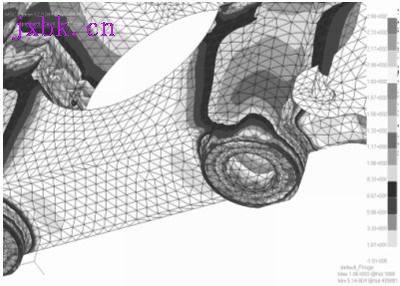
图16 框架局部应力分布 如图17~图19所示,为螺栓预紧力等于43KN时框架和缸体的应力(Von Mises stress)分布。 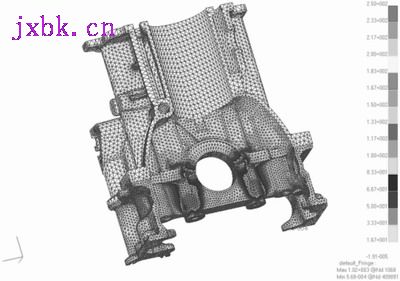
图17 框架和缸体的整体应力分布 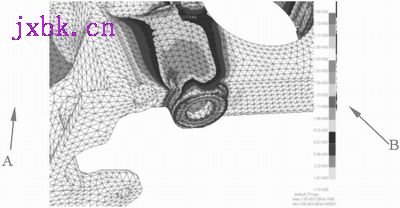
图18 框架局部应力分布 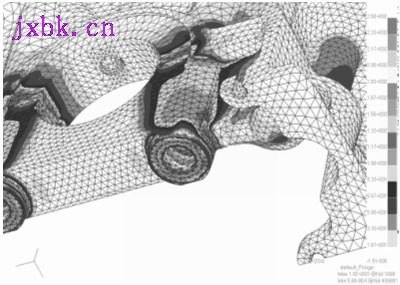
图19 框架局部应力分布 如上文中图14~图19所示,在框架与缸体之间以及螺栓与框架缸体接触面上压应力很大,这是由于计算是按照材料的弹性假设进行的,没有考虑材料的塑性变形,因此应力值很大,但不会引起失效。 如图15、图18和图16、图19所示,A处和B处应力值大于250MPa,超过了材料的强度极限,因此建议加大这两处的R值,以降低应力集中。在框架和缸体的其余部位,应力值都小于材料的强度极限250MPa,因此在此工况下强度满足要求。 如图20~图22所示,为轴瓦过盈量等于66μm框架和缸体的应力(Von Mises stress)分布。 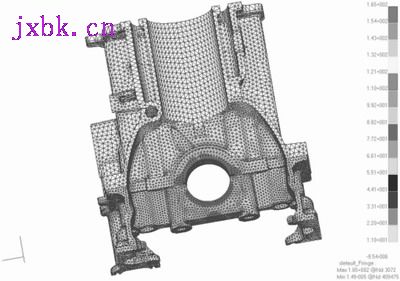
图20 框架和缸体的整体应力分布 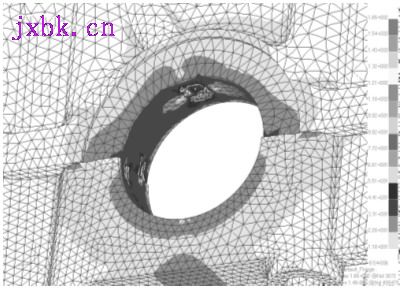
图21 框架和缸体局部应力分布 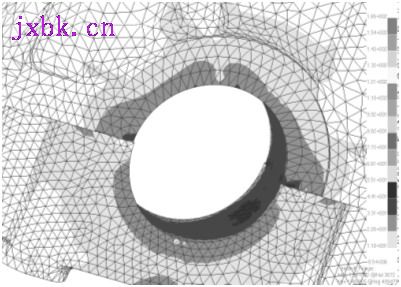
图22 框架和缸体局部应力分布 如图21所示,过盈量为66μm时应力最大值出现在缸体部分的油道孔处,应力值为165MPa,小于材料强度极限250MPa,满足要求。但是,还是建议此处的尖边增加倒圆,以降低应力集中。 如图23~图25所示,为爆压等于70bar时框架和缸体的应力(Von Mises stress)分布。 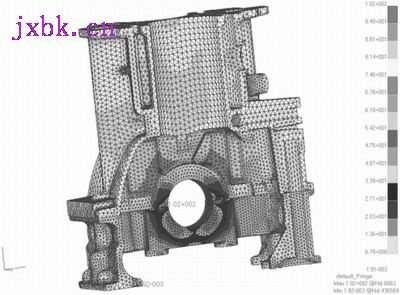
图23 框架和缸体的整体应力分布 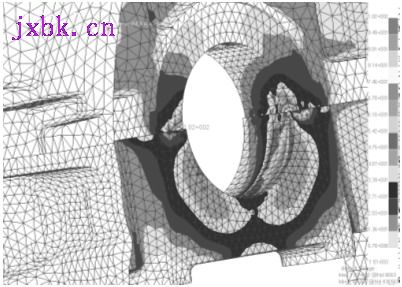
图24 框架和缸体局部应力分布 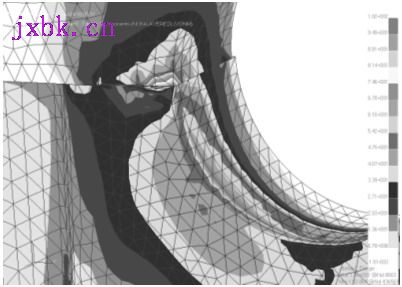
图25 框架和缸体局部应力分布 如图23~图25所示,应力最大值出现在缸体与框架接触的区域,其值为102MPa,小于材料强度极限250 MPa。 3.轴瓦的背压 轴瓦装配载荷工况下轴瓦的背压分布,如图26所示。 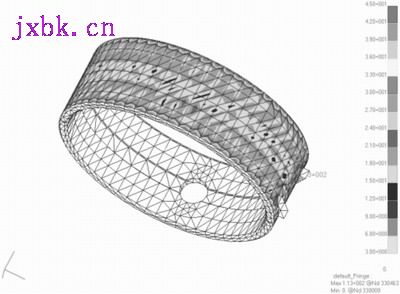
图26 过盈量为66μm时轴瓦的背压 如图26所示,轴瓦大部分区域的背压为12MPa~21MPa,这个压力已经足够阻止轴瓦与框架及缸体之间的相对移动。 五、结论 通过分析可得出以下结论。 1.如图15、图18和图16、图19所示,A处和B处应力值大于250MPa,超过了材料的强度极限,因此建议加大这两处的R值,以降低应力集中。 2.根据上述分析,框架和缸体的应力值在各工况下都小于材料的强度极限,满足静强度要求。 3.轴瓦孔的变形满足要求。 |