小型立式注塑机开关模动作故障之分析解决 |
|
日期:2007-7-23 23:16:24 人气:69 [大 中 小] |
|
|
在目前立式注塑机生产厂中普通反映所生产之10T至20T锁模力小型机存在如下故障: ◆ 在关模过程中,当机器从快速关模切换至慢速关模时出现较大的冲击和噪声,无论如何调节快速及慢速的压力值,均不能根除此故障。 ◆ 在开模过程中,会出现非常沉闷的噪声,通常开模动作的压力值要达到7MPa以上,动作速度慢且无论如何变化压力设定值的大小,动作速度均无明显变化。 在用户现场发现各生产厂所使用的油路原理均是一样的,全部采用单作用油缸加差动阀,油泵采用定量单泵加单比例溢流阀(如图1所示)。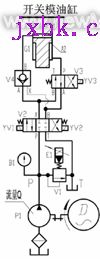 理论分析 立式机之关模动作流程为: 快速关模—>慢速关模—>高压锁模—>锁模停止。开模动作流程为快速开模—>慢速开模。快速关模时图1中V2阀之YV1线圈通电、V3阀之YV3线圈通电,比例阀V1之设定值为快速关模之压力值。此时G1之有杆腔的油液经过V3阀之P-B与V2阀P-A所供压力油一起经V4阀之A-B进入开关模油缸G1之无杆腔,这样即构成油压中所称的“差动回路”,当油缸G1之活塞杆直径越小时,如A2=(9/10)*A1,在同样供油流量时差动之速度可达到10倍非差动速度,但活塞杆越小则有杆腔面积A2越大,在供油压力相同情况下,差动关模时油缸产生的作用力只有非差动时的1/10,并且开模时开模速度也只有差动时的1/9,开模速度与差动关模速相差太大,两者相差越大在工作时越不合理,同时活塞杆太细油缸也难以设计加工并无法满足受力的需要。 实际设计中考虑具体使用环境等因素,A2/A1一般取在0.2-0.8之间,现对A2/A1分别为0.2、0.5及0.8时不采用差动合模及采用差动合模各种情况下之关模及开模时间计算如下: 设油缸直径D=120mm,油缸行程L=200mm,油泵流量Qp=28L/min,假定关模全过程全采用差动或全过程均不采用差动。 1、当A2/A1=0.2时,A1=113.04cm2,取活塞杆直径d=95mm,则A2=42.19cm2; A、不差动时,关模时间T1=L*A1/Qp=4.85S,开模时间T2=L*A2/Qp=1.81S; B、用差动时,关模时间T3=L*(A1-A2)/Qp= 3.04S,开模时间T2=L*A2/Qp=1.81S; C、不差动时开关模总时间T12=T1+T2=6.66S,用差动时开关模总时间T32=4.85S; D、用差动时节省时间为TT=T12-T32=1.81S。 2、当A2/A1=0.5时,A1=113.04cm2,取活塞杆直径d=85mm,则A2=56.32cm2; A、不差动时,关模时间T1=L*A1/Qp=4.85S,开模时间T2=L*A2/Qp=2.42S; B、用差动时,关模时间T3=L*(A1-A2)/Qp= 2.43S,开模时间T2=L*A2/Qp=2.42S; C、不差动时开关模总时间T12=T1+T2=7.26S,用差动时开关模总时间T32=4.85S; D、用差动时节省时间为TT=T12-T32=2.41S。 3、当A2/A1=0.8时,A1=113.04cm2,取活塞杆直径d=55mm,则A2= 89.30cm2; A、不差动时,关模时间T1=L*A1/Qp=4.85S,开模时间T2=L*A2/Qp= 3.83S; B、用差动时,关模时间T3=L*(A1-A2)/Qp=1.02S,开模时间T2=L*A2/Qp=3.83S; C、不差动时开关模总时间T12= T1+T2=8.68S,用差动时开关模总时间T32=4.85S; D、用差动时节省时间为TT=T12-T32=3.83S。 通过以上对比计算可以发现: ◆ 使用差动时,当关模行程与开模行程相同时,无论A2与A1的比值多少,开关模总时间均相同,在上述例子中T32均为4.85秒。 ◆ 开模时间则是A2越小,开模时间T2越短; ◆ 当A2/A1=0.5时,差动关模时间T3与开模时间T2相同,|A2/A1-0.5|越大,则T3与T2之差值也越大。 因此在设计差动油路时,如希望关模及开模速度基本相同,则应将油缸G1有杆腔的面积A2设计成等于无杆腔面积A1之1/2,即A2/A1=0.5,此时油缸的差动速度会达到无差动时的一倍,而开模速度也将等于差动之速度,控制油阀之选择只需选可以控制2倍油泵流量的阀门即可。 在实际的使用中,因为关模不可能是在全部行程范围内均为差动方式工作,而是在部分行程内执行非差动方式(即为了保护模具而进行的慢速关模过程)。为了使关模加开模之总时间最短,则应采取A2/A1较小的设计方案,在保证有足够的开模力的情况下,A2/A1越小越好,因为此种设计可保证使开模时间T2最短,同时也保证了开关模总时间达至最短。在目前各立式机生产厂也正是按此种方案设计的。但是此种设计又会带来油路设计上的其它问题,如果未引起重视就会产生前面所提到的故障现象。下面以某厂之15T机为例对此进行详细分析:
实例参数分析 ◆ 机器参数:合模力15吨,关模缸缸径为Φ120mm,活塞杆直径为Φ100mm,油泵流量为Qp=28L/min(排量19cc/rev,电机转速1480RPM)。则A1=113.04cm2,A2=34.54cm2。 如图1所示各油阀型号:V1阀为10通径单比例溢流阀 ;V2阀为G02-C2(6通径,额定流量40L/min) ;V3阀为G02-B2(6通径,额定流量40L/min) ;V4阀为CPDG-03(10通径,额定流量40L/min)。 ◆ 差动关模时油从V2阀之P→A,有杆腔之油液经差动阀V3之P→B,合并后油液经过V4之A→B,进入油缸G1之无杆腔,执行快速关模动作: 则V2之P→A流量Q21=Qp=28L/min V3之P→B流量Q31=12.32L/min(可以计算得到) V4之A→B流量Q41=Q11+Q12= 40.32L/min ◆ 慢速关模时压力油经V2阀之P→A,再经V4之A→B至G1无杆腔,有杆腔之油液经V3阀之P→A,再经V2阀之B→T回至油箱: 则V2之P→A流量Q22=Qp=28L/min V3之P→A流量Q32=8.56L/min(可以计算得到) V4之A→B流量Q42=Qp=28L/min V2之B→T流量Q24=Q32=8.56L/min ◆ 开模时压力油从V2阀之P→B,经V3阀之A→P至G1有杆腔,无杆腔之油液经V4阀之B→A,再经V2阀之A→T回至油箱: 则V2之P→B流量Q23=Qp=28L/min V3之A →P流量Q33=Qp=28L/min V4之B→A流量Q43=A1*Qp/A2=113.04*28/34.54=91.64L/min V2之A→T流量Q25=Q43=91.64L/min ◆ 差动关模时假设油压力为P1= 50Kg/cm2,则油缸G1在差动工作时产生之作用力为: F1=(A1-A2)*P1=(113.04-34.54)*50=3925Kg; ◆ 慢速关模时假设油压力也为P2=50 Kg/cm2,则油缸G1在慢关时产生之作用力为: F2=A1*P2=113.04X50=5652Kg; ◆ 慢速关模时如须产生与差动关模时相同的作用力,则慢速关模的压力值应设为P2=F1/A1=3925/113.04= 34.72kg/cm2;与差动关模之压力比为 0.7。 故障原因分析 通过以上的计算可以发现,在关模过程中油液流过V4阀之流量最大,为 40.32L/min,而V2及V3阀之流量均小于40L/min,用6通径换向阀及10通径液控单向阀可以满足使用要求。但是在开模过程中V2及V4之流量均达到 91.64L/min,远远超过6通径换向阀及10通径液控单向阀的额定通流能力,因此在做开模动作时必然会在G1缸的无杆腔产生具大的背压,在活塞上须产生较大的作用力才可克服此背压,这就是为什么要有7MPa以上的油压力才可开模的原因。同时因为在设计时从G1无杆腔至V2阀之A口及V2阀之回油T口油管直径一般均只有Φ6MM最大至Φ10MM,91.64L/min流量经如此小的管道及带节流作用的阀控口必须产生沉闷的噪声,这也解释了为什么在开模过程中,会出现非常沉闷如开老式拖拉机似的噪声。 当慢速关模的压力设定值与关模慢速时的压力设定值之比如等于0.7,此时两种工作方式下产生的作用力是相等的,那么机器从差动关模切换至慢速关模时作用在活塞上的力并未变化,为什么会产生噪声及冲击呢?
从图1中可以知道,此种系统所采用的是单比例溢流阀,即该系统只有压力是可以任意调节的,但是正因为只采用了单压力可调的比例阀(部分厂家也有用两台手调压力阀分别控制差动关模及慢速关模压力的方式),而流量却是固定的为油泵供油量,因此对两种工况下油缸G1的速度计算如下: A、差动关模时G1速度V11=Q41/A1=40.32*1000/60/113.04=5.95cm/s B、慢速关模时G1速度V12=Q42/A1=28*1000/60/113.04=4.13cm/s 可以发现,两种工况下之速度V11及V12是不同的,从差动关模方式切换至慢速关模时,即使通过设定压力使机器在G1上作用力相同的情况下进行切换,由于G1的速度从高速瞬时切换至低速,即G1之速度在差动切换至慢速时产生了跳变,同时因为在动作时序上使压力跳变与差动阀V3通电至断电切换同时进行,则必然使机器产生噪声及冲击! 结论 对使用差动油路的系统,必须在设计时对有杆腔进油无杆腔回油工况下之流量放大情况进行校验。所选择的控制油阀应能保证回油通路的通畅,而且还必须根据最大通流流量设计油缸无杆腔通油口直径、从阀块至油缸油管通径、阀块上油道通径等,减少回油阻力,才能使动作轻快平稳,同时节省能量减少系统发热,提高油压元件及密封件的使用寿命。在以上例子中我们为用户更改了设计,开关模换向V2阀选择使用G03-3C2,V3阀仍使用G02-2B2,而液控单向阀则选用了CPDG—06,并且加大相关通油管路。经在实际机台上使用,开模时压力降至30 Kg/cm2以下,而且动作平稳无任何异声。 差动关模切换至慢速关模时产生噪声及冲击,从上面分析中可知是因为速度产生了跃变引起的。为了消除这种跃变,有三个条件必须满足 :一是两阶段的压力速度设定值任意可调,二是当动作切换时,压力及速度均不能瞬间跃变,而应该是从一级压力速度按一定斜率渐变到另一级压力速度;三是压力流量的变化应与差动阀V3之切换分开进行。因此在实际使用中我们采用了如图2所示的油路,即V1用电液比例压力流量复合阀KEBG-02-40-C-30代替原单比例压力阀,并且使用立式机专用控制器KS3600,两者配合则完全满足了上述三个条件,基本消除了这种动作切换所产生的噪声及冲击 |
|
我有问题,我要进入论坛 |
出处:本站原创 作者:佚名 | |
|