罗新民1 , 陈康敏1 , 罗 刚2 , 范引鹤2 (1. 江苏大学材料科学与工程学院, 镇江 212013; 2. 南京航空航天大学能源与动力工程学院, 南京 210016 )
摘 要: 借助扫描电子显微镜(SEM)的专用拉伸台,通过取自相同焊接接头疲劳试件的原位拉伸试验和疲劳试验,分析了高温合金焊接接头原位拉伸的动态断裂过程,讨论了原位拉伸断裂行为与疲劳断裂的关系。结果表明,高温合金熔化焊接接头强韧性良好,断裂前应变可达17.5%,具有明显的形变强化效应;焊缝断裂形貌与应力状态密切相关,在平面应力状态下,裂纹形成于熔合区晶内缺陷和晶界交汇处,以延性剪切型断裂为主,在应力集中的棱角处,易诱发穿晶脆断;焊缝熔合区的微观组织不均匀性和焊趾应力集中的联合作用将使焊接接头在疲劳试验过程中发生应变硬化,引发疲劳裂纹。 关键词: 扫描电镜; 动态拉伸; 高温合金; 焊接接头; 疲劳强度
0 序 言 在高温合金的应用场合,焊接是重要的制造过程,焊接质量在整个焊接结构中起着决定性的作用。在使用过程中需承受交变载荷的高温合金焊接件,还必须进行疲劳校核。原位拉伸可对材料的微观破坏过程进行实时的动态观察,用取自相同焊接接头疲劳试件的试样进行原位拉伸,了解焊缝的动态断裂行为,并和疲劳试验结果进行比较,有助于提高对焊接接头疲劳破坏过程的认识,从而寻求改善焊接质量的有效途径。
1 试验材料和试验方法 试验材料为国产GH3030与GH150高温合金。 焊接试样制备:取厚度为2 mm的上述合金板,采用自动对接氩弧焊焊接, 焊丝为GH3128,直径为1.6~2.5mm,钨极直径2.0~2.5mm,焊接电流70~90 A,电弧电压12 V,氩气流量12~15 L /min,焊后经X光探伤检验。 在未经疲劳试验的焊接试样上截取原位拉伸试样,在垂直于焊缝的方向用线切割切取原位拉伸试样,焊缝处在试样中部,如图1所示。 试样经磨平,单面抛光并轻度腐蚀,以便观察组织的拉伸变形过程。 动态拉伸在JXA-840型扫描电子显微镜的附件SM-TS40专用拉伸台上进行,其最大拉伸载荷为2kN,加力传感器标定为150mV,电压与载荷呈斜率为1的线性关系。最大拉伸距离为20mm,拉伸速度可调,最大达50mm/min。动态拉伸中,可同时利用X射线能谱仪(EDS)对观测点进行元素分析。 焊接接头试样的疲劳试验在液压伺服疲劳试验机EHF-EG250KN-40L上进行,疲劳载荷采用轴向拉- 拉应力控制,正弦波脉动加载, f=4.5Hz,R=0.1。记录循环次数,检查疲劳断裂的发生部位。
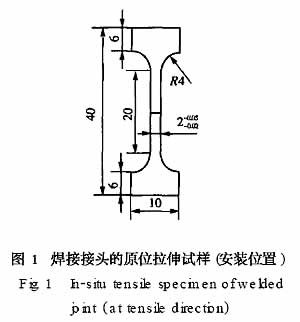 2 试验结果分析 2.1 焊接接头原位拉伸的宏观形貌 图2为焊接接头原位拉伸后期的宏观形貌。 焊缝是在非平衡状态下凝固的铸态组织,随匹配焊接材料的比例、与母材混合后的化学成分和冷却条件的差异,组织十分复杂 。如图2所示,原位拉伸过程中,在出现颈缩时,焊缝处呈现明显的变形不均匀性。这是由焊接接头微观组织不均匀性和复杂性造成的。说明试样在加载后,焊缝处微观组织在变形过程中,不同位向的晶粒组织及其内部位错运动导致试样对应部位组织继续变形所要施加的局部应力不尽一致,所以焊接接头呈现焊缝中央膨大,形成两段式颈缩的现象,符合板试样颈缩遵循的最小应变能路径原理。
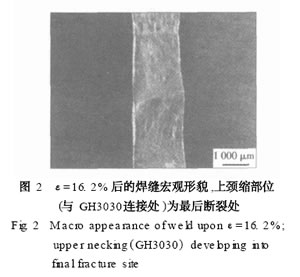 金相检查发现试件焊缝主要为树枝晶组织。有研究表明结晶前沿具有细树枝凝固界面的合金,其持久性能最佳,这种组织促使加工硬化,推迟了颈缩时间。母材是细等轴晶组织。熔合区组织比较复杂,与GH150 材交界处以大小不等的等轴晶为主,与GH3030材交界处以柱状晶为主。热影响区有局部晶粒粗化,因高温合金无同素异构转变。在焊接过程中, 除焊缝凝固组织外,与母材的过渡区因过热而呈不规则长大。这样,焊接接头的整体微观组织存在着3种取向各异的组织。因而接头存在着比较严重的微观组织不均匀性,它们必然影响接头的变形行为 。多晶体各晶粒变形时的相互配合是材料抵抗塑性变形的主要形式,否则极易在局部过早开裂。上述组织不均匀性易使焊接接头在疲劳性能试验过程中导致内部微观应力集中和各晶粒应变率的差异,最终将在较弱部位萌生疲劳裂纹。 2.2 原位拉伸中试样的微观变形过程 图3显示了在拉伸过程中试样表面的微观变形情况。 随拉伸进行,受力晶粒内存在的大量位错、层错等在应力的作用下,位错将开动,形成相互平行的滑移线,如图3a所示。塑性变形必须考虑加载速度,由于原位拉伸形变速率较低,晶粒形变比较均匀,滑移带平直、间距大小基本一致。但该图只显示了一个方向的滑移带,说明在均匀形变阶段,只有一个方向的滑移系占主导地位,此阶段合金将出现初始硬化 。随着拉伸进行,在其它晶粒中可以看到不同方向的滑移带出现,形成尖峰状或三角形。根据晶体学理论, <111>晶面是奥氏体的滑移面,也是层错形成面。该晶面有4个基本取向,每个晶面间的夹角理论计算为70°32′。如果某一晶粒截面和<111>平行或近似平行,由于<111>面上3个滑移方向的基准矢量间夹角为60°,是正三角形,所以拉伸时奥氏体晶内滑移线特征符合晶体学的位向关系。随着变形量加大,滑移带将逐渐变宽,并出现弯曲。
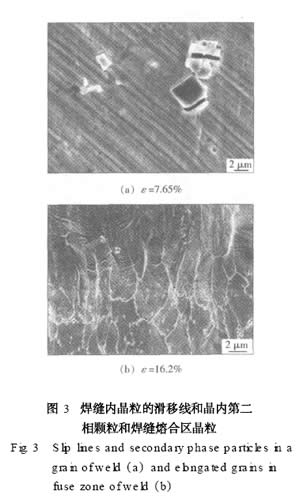 由于每个晶粒位向不同,并不是每个晶粒的滑移系的方向都与最有利于变形的方向一致,则造成各晶粒变形程度有差异。随着应变量增加,晶粒开始服从应力条件下的协同扭转,变形加剧,出现浮凸。从最初的只有少数区域的个别晶粒发生扭转,到最后几乎每个晶粒均都发生了扭曲,表面浮凸愈加明显,如图3b所示,在拉伸应力的作用下,焊缝熔合区的晶粒被明显拉长,出现择优取向。而其上方热影响区晶粒已出现滑移线粗化、弯曲。这种微观形貌变化可在一定程度解释宏观形变的不均匀性。同时发现在拉伸应力作用下,晶内脆性第二相颗粒(图中颗粒为氮化钛)与基体脱开,并碎裂,见图3a。这类第二相颗粒的滑移系少,在外加应力下易脆裂或沿边界断裂成为裂纹源,但有时也有利于提高材料的形变强化能力 。 不均匀组织如晶界、夹杂物等,也将对焊接接头的破断产生影响。从图4可见晶界和夹杂物在拉伸应力作用下对微观断裂机制的影响。由图4a可见,焊缝晶界在不大的应力水平下,就先于夹杂物发生开裂,但尚不能判断晶界析出物的影响。
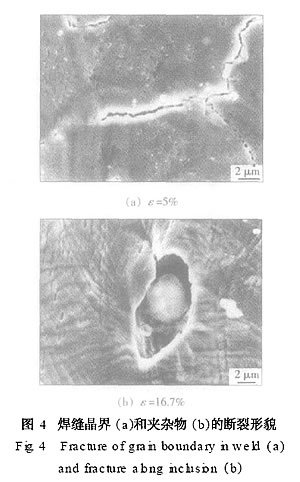 图4b显示的是夹杂物引起的裂纹源, X射线能谱分析显示,此类夹杂物主要是铝、钛或铌的化合物。原位拉伸显示出夹杂物从晶界或基体中脱落。由于夹杂物所致的应力集中,在孔洞的周围,将形成垂直于拉伸方向的显微裂纹。由此看出,在拉应力作用下,夹杂物及其周围组织是焊缝的薄弱环节。 2.3 裂纹的萌生 高温合金焊缝具有良好的强韧性配合,当试样发生颈缩现象后,由于板状薄试样在厚度方向不能造成变形约束,故不能形成平面应变状态,起始裂纹可在试样抛光表面直接观察到。表面一旦形成裂纹,则裂纹前端附近区域的变形亦基本不受约束,可以自由变形,呈完全屈服状态。在外力的作用下,裂纹前端由于塑性变形而沿试样厚度斜向和两侧呈张开状撕裂,与平面应力条件下薄板拉伸试样的宏观断裂行为一致。
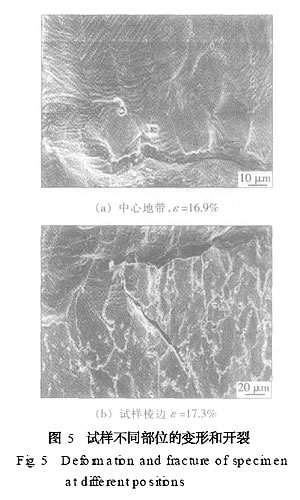 图5显示试样不同部位在原位拉伸中发生断裂的微观形貌和机制。 如图5a所示,在板状试样中心地带,滑移线粗化、弯曲;晶粒倾侧,呈现表面浮凸;因是平面应力状态,裂纹呈滑开型。而试样锐利棱角处应力状态复杂,易造成应力集中,少量塑变即发生形变强化,使进一步的塑性变形受阻,结果在试样边缘形成明显的脆性穿晶断裂,从其拉长的晶粒和表面滑移线可见其前期曾经历过塑性变形。 2.4 主裂纹扩展的原位观测 图6a~f为主裂纹萌生和扩展的原位观测结果。不同取向晶粒的变形能力和变形抗力是不同的,在拉伸载荷下,必然在取向最有利于滑移和微观内应力最易集中的晶粒先开始,组织愈不均匀,这种起始塑性变形的选择性就愈突出。当先变形的晶粒变形量超过一定值,就会萌生起始裂纹。如图6a所示,在一滑移三角形的尖端和孪晶界扭折底部,由于形变强化,材料变脆,产生一空洞,形成主裂纹源;空洞的产生,使应力状态软化如图6b所示,空洞在受力方向被拉长,并沿晶界向左撕裂,穿过孪晶界后,又产生一次生裂纹源;图6c表明孪晶被拉断,裂纹垂直于拉伸方向的部分更易滑开,主裂纹内侧又产生一次生裂纹;图6d表明新裂纹源不断出现,主裂纹已连结;图6e表明原观察点带出一第二相颗粒;主裂纹面局部有韧窝形成,同时出现新空洞,主裂纹的左侧前沿,向左侧快速撕开,进入全面溃退;图6f为试样最后断裂前的裂纹形貌。整个过程为:裂纹源形成,相互连结,形成主裂纹;主裂纹向斜上方滑移张开,撕裂面上可见蛇行滑移纹和小韧窝;随裂纹张开,不同性质第二相带出,脱离基体或碎裂;裂纹横向扩展以致最后断裂,其断口呈全剪切状,无放射区,为典型的平面应力条件下造成的切断型断口。
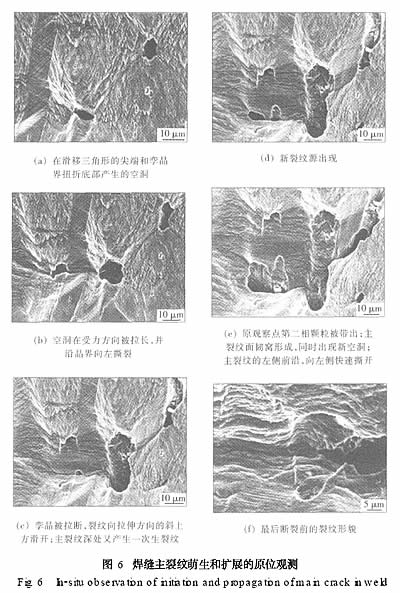 2.5 疲劳试验结果 表1 所示为两组焊接接头疲劳试验结果,每组含6个数据, S为子样标准差。试验结果表明,自动对接氩弧焊焊接高温合金的疲劳性能良好,低应力水平下的数据均匀性较优。疲劳断口检查发现,疲劳裂纹源始于焊趾或焊根处,同时发现疲劳源首先与焊缝表面微观质量有关,其次才是焊缝微观组织形态与结构。
|