回流焊温度曲线热容研究 曹白杨 赵小青 梁万雷 (北华航天工业学院电子工程系, 河北廊坊 065000) 摘 要: 本文全面的分析了回流焊温度曲线在回流焊工艺中作用, 回流焊工艺的工艺特点、影响回流焊温度曲线的各种因素。如何从热容的思想建立回流焊温度曲线的方法? 如何调整温度曲线通过控制温度曲线改善工艺过程, 减少回流焊工艺的缺陷? 关键词: 回流焊; 回流焊工艺; 回流焊温度曲线
回流焊接是表面组装技术(SMT) 特有的重要工艺,焊接工艺质量的优劣不仅影响正常生产,也影响最终产品的质量和可靠性。因此对回流焊工艺进行深入研究,并据此开发合理的回流焊温度曲线,是保证表面组装质量的重要环节。影响回流焊工艺的因素很多,也很复杂,需要工艺人员在生产中不断研究探讨,本文将从多个方面来进行探讨。
1 回流焊设备 在电子制造业中,大量的表面组装组件(SMA)通过回流焊进行焊接,按回流焊的热传递方式可将其分为三类:远红外、全热风、红外/ 热风。
1. 1 远红外回流焊 八十年代使用的远红外回流焊具有加热快、节能、运行平稳等特点,但由于印制板及各种元器件的材质、色泽不同而对辐射热吸收率有较大差异,造成电路上各种不同元器件以及不同部位温度不均匀,即局部温差。例如,集成电路的黑色塑料封装体上会因辐射吸收率高而过热,而其焊接部位———银白色引线上反而温度低产生虚焊。另外,印制板上热辐射被阻挡的部位,例如在大(高) 元器件阴影部位的焊接引脚或小元器件会由于加热不足而造成焊接不良。
1. 2 全热风回流焊 全热风回流焊是一种通过对流喷射管嘴或者耐热风机来迫使气流循环,从而实现被焊件加热的焊接方法,该类设备在90 年代开始兴起。由于采用此种加热方式,印制板(PCB) 和元器件的温度接近给定加热温区的气体温度,完全克服了红外回流焊的局部温差和遮蔽效应,故目前应用较广。 在全热风回流焊设备中,循环气体的对流速度至关重要。为确保循环气体作用于印制板的任一区域,气流必须具有足够快的速度,这在一定程度上易造成印制板的抖动和元器件的移位。此外,采用此种加热方式的热交换效率较低,耗电较多。
1. 3 红外热风回流焊 这类回流焊炉是在红外炉基础上加上热风使炉内温度更均匀,是目前较为理想的加热方式。这类设备充分利用了红外线穿透力强的特点,热效率高、节电;同时有效克服了红外回流焊的局部温差和遮蔽效应,并弥补了热风回流焊对气体流速要求过快而造成的影响,因此这种回流焊目前是使用得最普遍的。
随着组装密度的提高,精细间距组装技术的出现,还出现了氮气保护的回流焊炉。在氮气保护条件下进行焊接可防止氧化,提高焊接润湿能力,对未贴正的元件矫正力大,焊珠减少,更适合于免清洗工艺。
2 温度曲线分析与设计 温度曲线是指SMA 通过回流炉时,SMA 上某一点的温度随时间变化的曲线;其本质是SMA 在某一位置的热容状态。温度曲线提供了一种直观的方法,来分析某个元件在整个回流焊过程中的温度变化情况。这对于获得最佳的可焊性,避免由于超温而对元件造成损坏以及保证焊接质量都非常重要。
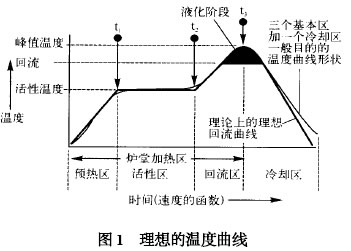 2. 1 温度曲线热容分析
理想的温度曲线由四个部分组成,前面三个区加热和最后一个区冷却。一个典型的温度曲线如图1 所示,其包含回流持续时间、锡膏活性温度、合金熔点和所希望的回流最高温度等。回流焊炉的温区越多,越能使实际温度曲线的轮廓达到理想的温度曲线。大多数锡膏都能用有四个基本温区的温度曲线完成回流焊工艺过程。
1) 预热区,也叫斜坡区,用来将PCB 的温度从周围环境温度提升到所须的活性温度。在这个区,电路板和元器件的热容不同,他们的实际温度提升速率不同。电路板和元器件的温度应不超过每秒2~5 ℃速度连续上升,如果过快,会产生热冲击,电路板和元器件都可能受损,如陶瓷电容的细微裂纹。而温度上升太慢,锡膏会感温过度,溶剂挥发不充分,影响焊接质量。炉的预热区一般占整个加热区长度的15~25 %。
2) 活性区,有时叫做干燥或浸湿区,这个区一般占加热区的30 ~ 50 %。活性区的主要目的是使SMA 内各元件的温度趋于稳定,尽量减少温差。在这个区域里给予足够的时间使热容大的元器件的温度赶上较小元件,并保证焊膏中的助焊剂得到充分挥发。到活性区结束,焊盘、焊料球及元件引脚上的氧化物被除去,整个电路板的温度达到平衡。应注意的是SMA 上所有元件在这一区结束时应具有相同的温度,否则进入到回流区将会因为各部分温度不均产生各种不良焊接现象。一般普遍的活性温度范围是120~150 ℃,如果活性区的温度设定太高,助焊剂没有足够的时间活性化,温度曲线的斜率是一个向上递增的斜率。虽然有的锡膏制造商允许活性化期间一些温度的增加,但是理想的温度曲线应当是平稳的温度。
3) 回流区,有时叫做峰值区或最后升温区,这个区的作用是将PCB 的温度从活性温度提高到所推荐的峰值温度。活性温度总是比合金的熔点温度低一点,而峰值温度总是在熔点上。典型的峰值温度范围是焊膏合金的熔点温度加40 ℃左右,回流区工作时间范围是20 - 50s。这个区的温度设定太高会使其温升斜率超过每秒2~5 ℃,或使回流峰值温度比推荐的高,或工作时间太长可能引起PCB 的过分卷曲、脱层或烧损,并损害元件的完整性。回流峰值温度比推荐的低,工作时间太短可能出现冷焊等缺陷。
4) 冷却区,这个区中焊膏的锡合金粉末已经熔化并充分润湿被连接表面,应该用尽可能快的速度来进行冷却,这样将有助于合金晶体的形成,得到明亮的焊点,并有较好的外形和低的接触角度。缓慢冷却会导致电路板的杂质更多分解而进入锡中,从而产生灰暗粗糙的焊点。在极端的情形下,其可能引起沾锡不良和减弱焊点结合力。冷却段降温速率一般为3~10 ℃/ S。
2. 2 按工作热容设计温度曲线 温度曲线的本质是描述SMA 在某一位置的热容状态,温度曲线受多个参数影响,其中最关键的是传输带速度和每个区温度的设定。而传输带速度和每个区温度的设定取决与SMA 的尺寸大小、元器件密度和SMA 的炉内密度。
作温度曲线首先考虑传输带的速度设定,该设定值将决定PCB 在加热通道所花的时间。典型的锡膏要求3~4 分钟的加热时间,用总的加热通道长度除以总的加热时间,即为准确的传输带速度。
传送带速度决定PCB 暴露在每个区所设定的温度下的持续时间,增加持续时间可以使表面组装组件接近该区的温度设定。
接下来必须确定各个区的温度设定。由于实际区间温度不一定就是该区的显示温度,因此显示温度只是代表区内热敏电偶的温度。如果热电偶越靠近加热源,显示的温度将比区间实际温度高,热电偶越靠近PCB 的直接通道,显示的温度将越能反应区间实际温度。
速度和温度确定后,将参数输入到焊炉的控制器,从而调整设定温度、风扇速度、强制空气流量和惰性气体流量等。炉子稳定后,可以开始作曲线。一旦最初的温度曲线图产生,可以和锡膏制造商推荐的曲线进行比较。
首先,必须确定从环境温度到回流峰值温度的总时间和所希望的加热时间相协调,如果太长,按比例地增加传送带速度,如果太短,则相反。 下一步,图形曲线的形状必须和所希望的(如图1 所示) 相比较,如果形状不协调,则同下面的图形(如图2~5 所示) 进行比较。选择与理论图形形状最相协调的曲线。应该考虑从左到右(流程顺序) 的偏差,例如,如果预热和回流区中存在差异,首先将预热区的差异调整,一般最好每次调一个参数,在作进一步调整之前运行这个曲线设定。这是因为一个给定区的改变也将影响随后区的结果。
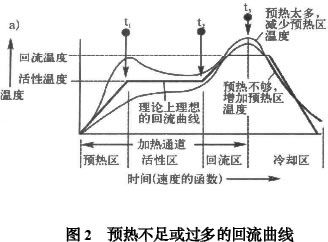
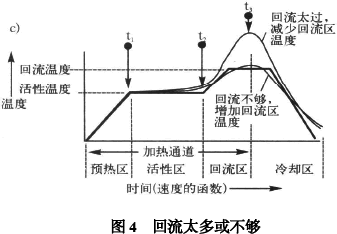
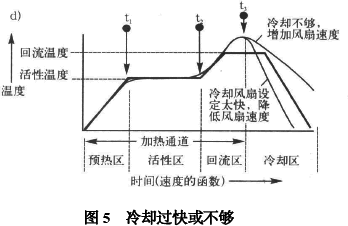 当最后的曲线图尽可能的与所希望的图形相吻合,应该把炉的参数记录或储存以备后用。
在作实际温度曲线之前,需要准备下列设备和辅助工具:温度曲线测试仪、热电偶、将热电偶附着于PCB 的工具和锡膏参数表等。
测量回流焊温度曲线时需使用温度曲线测试仪,其由测温仪和微型热电偶探头组成。测量时,微型热电偶探头可用焊料、胶粘剂、高温胶带固定在测试点上。热电偶附着的位置也要选择,通常最好是将热电偶尖附着在PCB 焊盘和相应的元件引脚或金属端之间(如图6 所示) 。打开测温仪上的开关,测温仪随同被测印制板一起进入炉腔,自动按内编时间程序进行采样记录。测 |