近年来,随着计算机网络的发展,企业资源计划(ERP)的应用已日渐普及,制 造执行系统(MES)的研究和应用也得到业界的高度重视。感应热处理机床是一种清洁热处理 设备,符合现代化工业生产的3S标准(Sure—可靠,Safe—安全,Saving—节约),又可以安 装在生产线上进行在线金属热处理,在国内外机械热处理行业已广泛应用,在制造多功能回 转式淬火机床时,笔者研制了支持现场总线的数控系统使机床支持工业以太网,进而可以与 车间级网络进行信息交换,并进行远程淬火参数设置。 1多功能回转式淬火机床简介 感应加热是利用电磁感应的方法对导体材料进行加热。其主要优点是 “效率 高、成本低、节能、易于实现自动控制。金属热处理的感应加热设备主要包括:加热电源、 感应热处理机床、感应器和淬火变压器。 多功能回转式淬火机床是一条具有完善保护功能的自动加工线,采用回转式结构,使上、下 料在同一个工位位置完成,操作方便;该机床可以同时加工同一种零件上的3个不同表面, 做到一个工件在一台淬火机床上一次完成淬火,且每个加工工位参数设置有一定的柔性冗余 ,可以实现各种淬火方式,如同时、连续、连续同时以及多段淬火等,主要应用在汽车、摩 托车制造行业,以满足其多品种、小零件的淬火处理。 1.1一体化设计 为了减少占地面积和安装周期,采用一体化设计,即将机床与淬火液循环系统、冷 却液循系统、加热电源和淬火变压器集成于一体,其层次结构如图1所示。 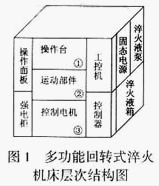
从图1可以看出,在高度方向上该机床结构分为3层,上支板以上为转盘、夹 具、淬火液回收槽等,上支板①与中支板②之间为运动部件,中支板②与底座③之间为执 行部 件(电机)和减速机。这种结构形式能有效地防止淬火剂对某些机(电)部件的不良影响,同时 便于部件的拆装维修。 1.2生产线化 多功能感应淬火机床采用9工位回转式结构,其中3个工位为加工工位,图2为工位 分布及流程示意图,图中A、B、C为3个上下料工位,A′、B′、C′ 为3个加工工位,可以对同一个工件的3个不同部位进行淬火(回火),也可以对3个 不同的工件或3个相同的工件进行独立淬火(相当于3台机床),转盘可以分度40°、80°、12 0°以适应不同工件的淬火要求。 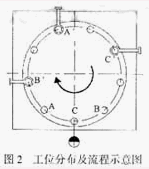
2数控系统设计 多功能回转式感应淬火机床要求: ①3个加工工位同时独立运行; ②连续淬火 时速度连续变化不停顿; ③具有3个工位下降不到位和转台不到位自纠正功能。常规的数控 系统无法满足这些功能,现自行研制的基于工控PC的数控系统,在Windows 2000下利用线程 技术实现了上述功能。 2.1硬件总体设计 图3给出了系统总体设计框图,3个工位的工件升降定位由步进电机控制,3个 工位的旋转由变频器控制,转台分度及定位由步进电机控制。 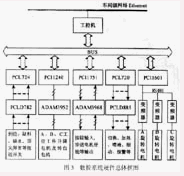
工控PC是系统的核心,一方面对机床各运动部件进行检测与控制,另一方面通过网卡与车间 级网络相连,使系统可以利用远程计算机输入淬火参数,也可以显示机床工作情况;PCI-1 240用于步进电机速度和定位控制,同时检测步进电机各种异常信号;PCI-1751为48路TTL 电平并行输入输出板,其中32路设置为输入,用于操作按钮输入,包括启动、暂停、急停按 钮,3个工位手动加热、喷液、旋转、切换,转台快速正反转、慢速正反转,3个工位工件快 速上升下降、慢速上升下降等;16路设置 为输出,用于转台及3个工位步进电机使能控制。PCL-724为TTL电平输入板,用于对到位、 缺料、缺水、顶尖异常等信号进行检测,由于板上无电平转换和信号隔离功能,而接近开关 为24 V,所以使用PCLD-782作为输入电平转换和信号隔离电路;PCLD-885为16路高功率 继电器输出板,具有极强的输出驱动能力,触点容量为交流220V 5A;PCL720为64路开关量 输 入输出板,在这里主要与PCLD-885一起,控制各工位切换、加热、喷液、吹堵、回火。 PCI-1601为RS232转RS485接口板,主要用于与变频器FR-E500连接,控制工件旋转电机的 转速,并监视变频器的运行状态,其连接线路如图4所示。 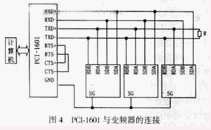
图4中R为终端匹配电阻,阻值为100 Ω。由于传送速度和传送距离等原因, 有可能受到反射的影响,故设此电阻。 2.2软件设计 系统软件设计主要考虑软件的通用性、可靠性和易用性。为此着重考虑以下几个问 题: ①3个工位独自使用加热电源以及3个工位共享加热电源时切换功能; |