(4) 设计技巧。由于大型罐车产品的装配体包含几百甚至上千的零件,因此在设计过程中必须对零件进行适度的“简化”处理,否则产品的总装配体的动画仿真甚至只是简单的旋转都非常缓慢。因此在不影响整体效果的前提下,采用了如下两种方法进行处理以提高设计效率: 1)装配体中的零件显示方式有实体、线框等方式(甚至可以用参数控制零件在装配体中是否显示),对于有些非关键零件可以忽略其内部形状及细节描述,这样可以有效地降低对于计算机硬件的要求,从而使大型装配体的显示操作变得快捷而且逼真; 2)用图层设置对大装配体中的零、部件进行分类管理(单个零件的设计也应对实体、基准面及草图等相应地进行分层管理),这样对于图形显示、编辑及动画模拟等都重要的意义。零件、部件间的装配信息可以利用SolidWorks软件的Property Manager来获取,从而检查是否按照其应有的装配约束(如贴合、对齐、同轴等)进行了正确的装配操作。 四、应用实例 基于以上的设计思路及技术手段,我们在产品设计过程中采用了三维的全参数化设计方法,相对于传统的手工绘图设计及二维软件设计,不但提高了设计效率,而且提高了设计的准确性,从而实实在在地提高了产品的市场竞争力,为企业的发展注入了新的活力。 下面以我厂主导设计的铁路卧式粉状货物罐车为例,来说明其零件的参数化设计及产品的装配设计方法。 图2为罐体的参数化3D模型。罐体的主要功能是运输及装卸货物,需根据自重、载重、工作压力等来设计罐体的长度L、半径r及壁厚δ,同时设计时要考虑到它与几个盖板间的装配关系,将其作为其他零件的父零件来处理。在模型中同时建立用于装配的基准轴和基准面,而且这些特征也都是参数驱动的,并放在专用图层中。 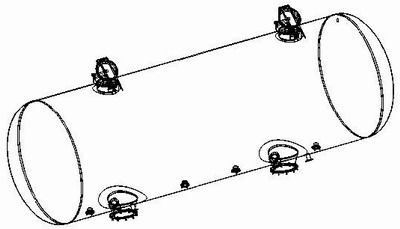
图2 罐体的参数化3D模型 图3为罐体与枕梁上盖板、牵引梁上盖板的装配图。两个盖板零件在装配树中都以罐体为其父节点,在进行参数化建模时,除了模型本身的参数驱动外,还应建立其与父零件(罐体)之间的参数关联:枕梁上盖板及牵引梁上盖板的半径等于罐体半径加上罐体壁厚。同时建立用于装配的基准轴及基准面,在进行装配建模时,通过与罐体的轴向同轴约束及基准面的贴合约束,就可以建立参数化的装配模型,同时罐体半径的改变可以传递并且驱动两个盖板模型的更新。 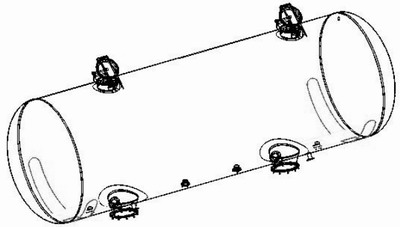
图3 罐体与枕梁上盖板、牵引梁上盖板的装配图 图4为罐体装配与车体其他部分的最终装配效果。由于在零件建模时采用了图层管理及良好的参数控制,因此装配校验变得非常简单而且明晰,通过图层的关闭、装配树中对零件的抑制与反抑制等方法来控制零件及部件(专用和通用)的显示,通过参数的关联、传递、模型驱动及IPA方法来检验设计结果,从而保证零件设计与装配设计之间的协调一致,并且通过IPA动画模拟还避免了部件之间可能发生的干涉。 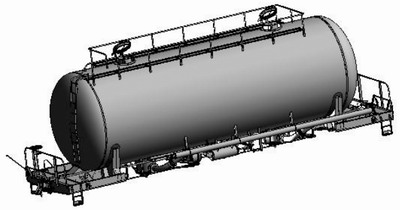
图4 罐体装配与车体其他部分最终装配效果 五、结论 通过CAD软件及相关设计技术的应用,我厂的产品设计周期大大缩短,设计质量也得到了显著提高,从而提高了本企业产品的市场竞争力,取得了显著的社会效益和经济效益。
|