基于多参量状态信息融合的刀具磨损状态智能识别 |
|
日期:2007-8-25 22:52:07 人气:60 [大 中 小] |
|
|
1 概述刀具磨损是金属切削过程中必然发生的现象,现场统计证明,刀具失效、破损是引起NC类自动化加工机床利用率下降、生产成本提高的首要因素,是机床设备和切削加工安全事故的重要起因,由其引起的停机占故障停机时间的1/5~1/3。因此开展刀具磨损的在线检测在自动化加工中具有极其重要的现实意义。 刀具状态的检测方法主要有直接法与间接法。直接法是直接检测刀具磨损面的数值大小;间接法是通过检测与刀具磨损状态相关的物理信号来估计刀具磨损状态。当前的各种监控技术主要是集中于间接检测。其中最为常见也较为有效的有切削力检测、声发射检测和电机电流/功率检测等。切削力一直是表征切削过程的最重要的特征,切削过程的变化都是和切削力密切相关的,所以用切削力监测刀具状态有着灵敏度高、抗干扰性好等较为突出的优点。刀具的磨损量不仅与加工工况相关,而且与刀具使用时间的长短有着密切的关系。 本文主要从实用的角度出发,建立了基于切削力和基于相对切削时间的两种磨损模型。切削力模型是利用回归算法和模糊分类技术建立的,该模型描述了切削力、切削参数与刀具磨损状态之间的关系,通过检测切削力信号可在线识别刀具磨损状态。基于相对切削时间模型利用回归技术直接建立刀具磨损量与切削参数及时间的关系,可在较大的切削条件变化范围内实现对刀具磨损的识别。 2 两种磨损识别方法理论模型的建立当加工过程中出现故障时(如刀具磨损或破损),将导致加工状态信号的变化。因此传统的监控系统都是从检测的状态信号的特征参量的变化中获取故障特征,进而实现对加工状态故障的识别与决策。但是,在加工过程中由于切削参数的变化也将引起加工状态信号的变化,这种变化往往比由加工故障导致的加工状态信号的变化要大得多。传统的监控系统由于未能很好考虑切削条件变化对加工状态信号的影响而只能监视单一工况下的加工过程,而无法用于先进制造中切削条件多变的加工过程。就此,作者一方面利用模糊回归网络技术,根据磨损量建立了基于切削力信号的数学模型,利用切削力信号间接判断刀具磨损状态;另一方面,利用回归技术,基于相对切削时间建立了刀具磨损量与切削参数及相对切削时间的数学模型。
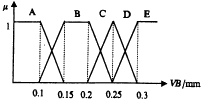 图1 刀具磨损状态隶属度函数- 磨损状态模糊分类
- 刀具磨损是相对缓慢的过程,通常磨损过程分为3个阶段,即初期磨损阶段、正常磨损阶段和急剧磨损阶段。三个阶段属于不同的磨损状态,各状态间的界限有一定的模糊性和重叠性。对于自动化加工而言,检测刀具磨损量不一定要精确的量,只要知道其在一定的磨损范围内即可。针对铣削,磨损状态很复杂,根据铣削过程的要求及实验数据,把刀具磨损状态分为A、B、C、D、E五类,各类的平均磨损量分别为:0.1mm、0.15mm、0.2mm、0.25mm、0.3mm。根据磨损状态的模糊性,建立如图1所示的磨损状态隶属度函数。之所以选择B类为梯形是因为正常加工时,在此区间其模糊程度相对要求低些。
- 基于切削力信号磨损模型
- 切削力是表征切削过程最重要特征的物理量。在切削过程中所产生的多数变化都和切削力密切相关。大量研究证明,随着刀具磨损的增加将导致切削力增大,刀具破损将引起切削力幅值的骤变。切削速度v、进给速率f、切削深度ap的变化都会影响切削力的大小。同时,切削力的大小也随工件材料、刀具材料等具体切削环境的不同而有所不同。根据金属切削原理,对于新刃刀具切削力与切削用量的关系有如下公式: F=Cvxfyapz (1)式中:C——决定于刀具几何尺寸和材料性质的系数;
- x,y,z——切削用量的指数。
- 式(1)表示了加工过程中切削力同各切削参数的关系,该切削力模型属于静态非线形模型,经线形化后,模型变为: InF=InC+xInv+yInf+xInap (2)
- 针对不同磨损状态刀具,在A、B、C、D、E五类中,相应的有如下表示式:
- A类:Sa=InFa=a11+a12Inv+a13Inf+a14Inap
- B类:Sb=InFb=a21+a22Inv+a23Inf+a24Inap
- C类:Sc=InFc=a31+a32Inv+a33Inf+a34Inap
- D类:Sd=InFd=a41+a42Inv+a43Inf+a44Inap
- E类:Se=InFe=a51+a52Inv+a53Inf+a54Inap
(3)- 利用矩阵形式表达为: S=W*X (4)
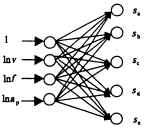 图2 切削力模型网络示意图- 式(4)可以用图2的神经网络形式来表达。对该网络模型不采用传统的BP算法来调节权重值,而是直接利用回归技术来调节权重值,这是由于该网络输入输出之间的关系已经是线性的,而且基于回归的神经网络的学习速度快,可以在线学习识别。
- 切削力模型是以切削力幅值为模型的特征值,在已知v、f、ap的情况下,利用式(3)推得Fa、Fb、Fc、Fd、Fe作为图1中的模糊聚类的中心,将检测到的切削力值与聚类中心比较,从而来确定当前刀具磨损隶属度而达到检测目的。
- 基于相对切削时间的磨损模型
- 根据加工过程中刀具磨损规律的先验知识可知,刀具磨损量随加工时间的发展而变化。在不同的切削条件下,增长的快慢不同,研究发现,在同一切削条件下,磨损量的变化率近乎是一定值,但基于实际工
|
|
我有问题,我要进入论坛 |
出处:本站原创 作者:佚名 | |
|