切削过程中“扎刀”现象的理论分析及其预防措施 |
|
日期:2007-8-20 21:17:22 人气:34 [大 中 小] |
|
|
1 引言
由于受系统刚度和切削阻尼的影响,在金属切削加工过程中会产生失稳现象。由负阻尼引起的失稳现象称为动态不稳定,由负刚度引起的失稳现象称为静态不稳定。笔者以机械加工过程中提高产品质量、降低成本消耗为目标,对金属切削加工过程中因刀具变形引起负刚度而造成的静态失稳现象进行了分析研究,揭示了金属切削过程中“扎刀现象”的本质,并提出了在生产实践中防止产生“扎刀现象”的有效措施。
2 切削时的“扎刀”过程
以刨削加工为例(如图1所示)分析加工过程中产生的“扎刀现象”。刨削加工时,工件以速度V从左向右作主运动,工件表层厚度为s0的一层金属被刀具切下,切削力为P0。在P0的作用下刀具产生弹性变形,图中刀刃位置由未切削时的O点移到了O'点。此时刀具的弹性恢复力Fs与切削力P0相平衡。但这种平衡是暂时的、不稳定的。切削过程中任何偶然的、微小的干扰都会打破这种平衡。例如刀刃切到工件材料上的某一硬质点,切削力P0马上获得一个增量dP。在dP的作用下刀刃再由O'移到O"点处。此时刃口因刀具变形向后移动了dx,且下降了ds。ds使切削厚度产生一个同样数量的瞬时增量,而切削厚度的增加又再度引起切削力的增大,使得刀具刃口进一步下移,刀尖则越来越深地扎入工件。如此循环的结果会使刀尖因迅速增大的切削力作用而产生崩刃。我们把金属切削加工过程中出现的这种现象称为“扎刀”。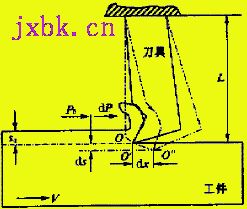 图1 3 “扎刀现象”的理论分析
图1所示的切削系统显然是一个具有位移的反馈系统,此系统可由框图2表示。图2中上面的框图为刀具系统,其输入量是作用在刀具上的切削力的变化量dP,而输出量是刀刃由此产生变形后的水平位移量dx;下面的框图表示切削力的控制机构,输入量是dx,输出量则是刀刃因水平位移后切削力的变化量dP,dP再反馈作用于刀具系统。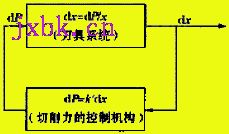 图2 若将图1所示的切削系统顺时针转过90°,则可将刀具近似地视为一悬臂梁(其简图见图3)。设刀具的装夹是完全刚性的,由材料力学可知刀具的刚度为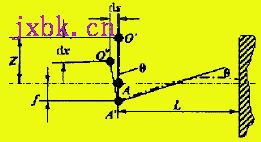 图3 k=dP=L3dx3EI(1) 式中 L——刀具的悬伸长度 EI——刀具材料的抗弯刚度
由位移反馈所产生的等效刚度k'可由以下方法求出:首先求出图1中刀刃的水平位移量dx与其垂直伸长量dx(亦为切削厚度的增量)之间的关系。忽略刀具的自重,因刀杆为一悬臂梁,端部作用有一集中载荷dP,则其端部的挠度f和转角q分别为
f=dPL33EI(2)q=dPL22EI 在图3中,设刀刃到刀杆的中性面间的距离为Z,且假设中心面端点A仅在铅垂线上移动,即由A点到A'点,则有
dx≈=fAA'(3) 由图3中的几何关系可知ds=qZ,代入式(2)、式(3)可得
ds=3Zdx2L(4) 此外,将切削力! 与切削厚度$ 之间的函数关系P(s0+ds)在s0附近展成幂级数
P(s0+ds)=P(s0+dP(s0)ds+……ds 则切削力的增量为
dP=P(s0+ds)+P(s0)=ksds+……(5) 式中ks=dP(s0)/ds,因为P(s0+ds)是ds的增函数,故应有ks>0。
将式(4)代入式(5)并略去高阶微量,得
dP=ks3Zdx2L 由此得到等效刚度系数为
k=dP=ks=3Zdx2L(6) 则系统的总刚度为
k-k'=L3-ks3Z3EI2L(7) 式中,-ks·3Z/2L是由于位移反馈造成的等效负刚度。
显然,产生“扎刀现象”的条件为
(L3-ks3Z)<03EI2L(8) 4 “扎刀”的预防措施
由上述分析可知,若将式(8)中的-ks·3Z/2L(即由位移反馈造成的等效负刚度)变为正刚度,便可防止产生“扎刀”现象。在生产实践中,通常通过改变刀杆形状来防止出现“扎刀”现象。
1) 刨削加工时,将直头刨刀改为弯头刨刀(如图4所示)。当刀杆向右弯曲变形时,切削刃同时退离工件的已加工表面,可避免“扎刀”。 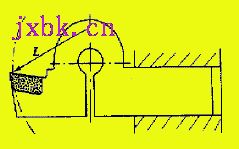 图4 图5 2) 车削加工时,将刚性直刀杆改成具有弹性的圆弧形弯刀杆(如图5所示)。采用此类结构的车刀加工时,其切削刃口在切削力的作用下基本上沿一圆弧转动,从而退离工件时可防止因“扎刀”而产生崩刃现象。这种弹性结构的车刀多用于工件的切槽加工,尤其在切断加工时显得非常实用。
作者单位:湖南工程学院 |
|
我有问题,我要进入论坛 |
出处:本站原创 作者:佚名 | |
|