以提高加工效率 促使制造成本降低 |
|
日期:2007-8-13 21:08:41 人气:54 [大 中 小] |
|
|
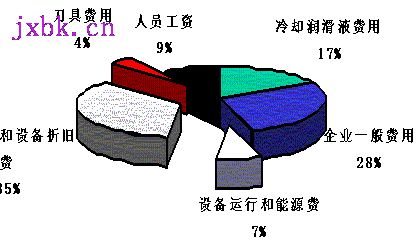 图1 德国汽车零件加工的单件成本构成示意 |
中国加入WTO以后,正在逐渐成为世界性的制造基地。摆在中国的机械制造业尤其中国汽车制造业面前的一个问题,就是如何降低制造费用,提高经济效益和产品的市场竞争力。这一问题将直接影响汽车制造业的生存和发展。各汽车制造商便千方百计,想尽一切办法来实现这一目标。在这样的条件下,我们作为刀具商能够为制造商做点什么来与制造商一起降低生产成本,共同迎接WTO的挑战呢?
那么,我们首先应该如何着手来降低制造费用呢?图1是对德国汽车零件加工的单件成本构成的示意。我们可以发现,与加工效率有关的人员工资、企业一般费用、设备运行和能源费、利息和设备折旧费4项的总和,占到制造成本近80%。
因此,提高加工效率应该成为我们降低制造成本的首选。从德国制造业的统计来看,刀具而言,降低刀具采购价格30%,大约可以降低制造费用1%,延长刀具寿命50%,同样可以降低制造费用1%,而提高加工效率20%,则可以降低制造费用约15%。
如何实现加工效率的提高呢?作为刀具制造商而言,应该认真研究制造业的需要,努力研制适合制造商生产发展的新产品,则是每时每刻都必须重视的主要问题。
总体上说,提高切削效率主要还是通过提高切削参数的三方面来实现:
1. 提高切削速度
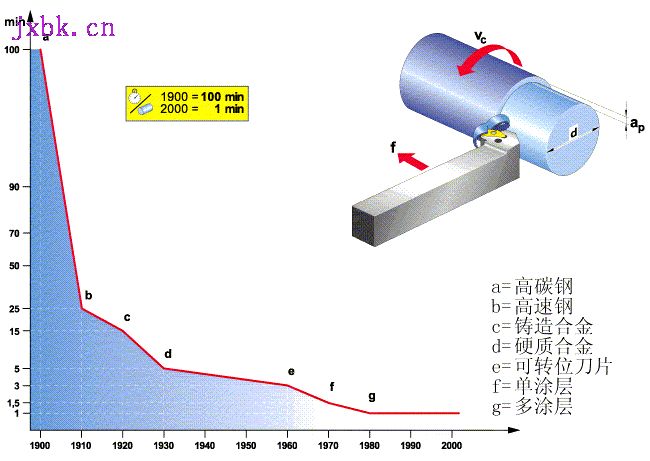 |
我们可以回顾一下,刀具的发展历史实际上就是切削技术不断进步的历史。高速钢、硬质合金、镀层等新技术的出现和发展,构成了切削技术领域的一个个重大的里程碑。这样的飞跃每一次都使制造商们获益匪浅。
在100年以前,人们主要应用高碳钢进行切削加工。通过高速钢、粉末冶金、硬质合金、可转位、单镀层、复合镀层等发展,加工效率的提高十分惊人。可以说,100年前需要100分钟加工的工件,现在只需要短短1分钟即可完成。
采用新技术复合镀层的可转位刀具就单价来说,可能比较高,但其提高加工节拍所带来的经济效益常常同样会令使用者获益匪浅。笔者曾经在一阀门制造企业推广可转位钻头,他们的有关人员担心可转位钻头的价格会使他们不堪承受,但通过试验和经济分析,他们充分认识到了使用新技术刀具能够为他们创造的价值。
高速钢钻头与可转位钻头的分析对比
| 高速钢
| 浅孔钻
|
价格
| 150.00
| (刀片)34.00 (刀体)2,500.00
|
切削速度(m/min)
| 18
| 160
|
进给量(mm/r)
| 0.38
| 0.12
|
转速(r/min)
| 191
| 1,698
|
进给速度(mm/min)
| 72.6
| 203.7
|
单位工件钻孔时间(min)
| 16.5
| 5.9
|
单位工件机床成本
| 41.3
| 14.7
|
可刃磨/转位次数
| 20
| 4
|
每次刃磨间成本
| 7.50
| 17.00
|
每次刃磨间寿命(m)
| 2.5
| 10.0
|
每次刃磨间加工工件数
| 2
| 8
|
单位工件刀具费用
| 3.75
| 2.13
|
单位工件总成本
| 45.09
| 16.85
|
试验背景数据:
直径(mm) 30
机床每小时成本 150
钻孔深度(mm) 100
单位工件钻孔数 12
日产量 200
年产量 72,800
|
| 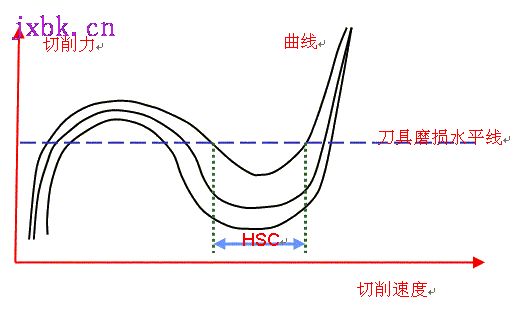 图3 高速切削应用区间
|
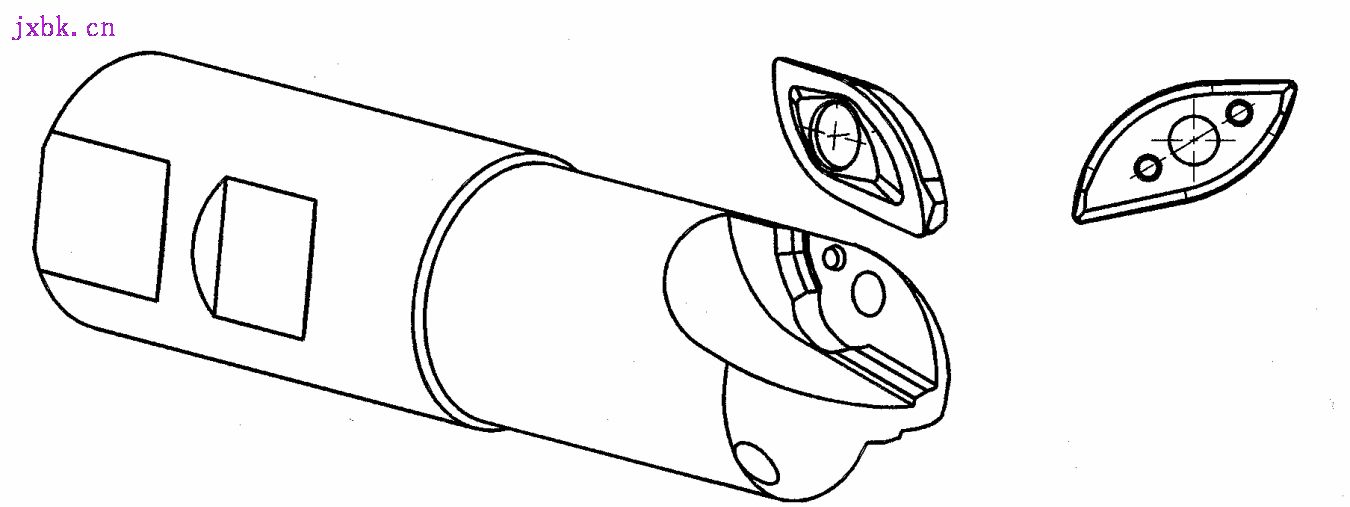 图4 F2339的空刀窝起到很好的卸载作用 |
可以看到,虽然可转位刀具的刀体成本较高,但每个工件节约28.24元,刀体费用仅需加工89个工件!
目前,高速切削(HSC)已经越来越成为中国制造业提高加工效率的选择。二十世纪八十年代以来,欧美刀具业经过大量的试验研究,对切削机理的认识有了新的突破,即当切削速度的提高超过某个临界值 (不同材料有不同的临界值)后,刀具的磨损并非按照泰勒曲线的规律急剧增加,反而在以后的一个区间内随切削速度的增加而有所减少,在经历一个谷底后再重新上升。虽然这一现象的理论解释尚未得到统一,但这并不妨碍我们在那个谷底附近对高速加工技术进行应用。按目前看,工业发达国家的航空,汽车、动力机械、模具、轴承、机床等行业首先受惠于该项新技术,使上述行业的产品质量明显提高,成本大幅度降低,获得了市场竞争优势。
理论分析和实践证明,高速切削是一个系统工程。从技术的层面上,它涉及高速主轴单元、快速进给和高加(减)速度的驱动系统、高性能的快速CNC控制系统、高刚性的机床结构、数据的处理和传送、动平衡控制、超硬刀具材料和镀层工艺技术等;从管理的层面上,它涉及高速加工理念、新的管理方法等。作为系统的一部分,各个环节只有互相协调,才能发挥其应有的效益。例如,加工模具中的曲面,如果其它环节都符合了高速加工的要求,但其CAM的数据处理只使用直线插补而不是圆弧插补或样条曲线插补来模拟工件表面的曲线,机床的进给系统总是处在不停的加减速过程中,就无法达到预定的进给速度,从而限制了切削效率的提高和生产成本的降低。同样,如果您在高速铣削中选用了普通结构的整体硬质合金三刃立铣刀,由于其通常采用一齿过中心的结构,动平衡性能先天不足,同样也会不能达到您的预定转速,使您的加工效率无法达到预定目标。同时,铣削类回转刀具在高速旋转时各部分都要承受很大的离心力,其作用远远超过切削力的作用,成为刀具的主要载荷,离心力过大足以导致刀体破碎。因此,我们在高速切削中首先应充分重视刀具安全性问题。为了安全,德国标准规定刀具产品在至少超过厂家标称的最高转速60%的情况下才能发生位移,在至少超过厂家标称的最高转速100%的情况下才能发生解体或整体刀具的折断。在实际应用中,瓦尔特在其2000年的综合样本上,列出了其几乎所有的扩孔、镗孔刀具和铣刀在不同直径下的的最高转速,在使用规定的其原产刀片和原产配件的条件下是非常安全的。现在,欧美刀具厂商越来越多地在设计阶段就考虑对高速切削的适应性。如瓦尔特的一部分新刀具如球头铣刀F2339,刀片底面有两个空刀窝,可与刀体上的凸起相配合,对作用在夹紧螺钉上的离心力起卸载作用,使其可以采用相对较高的切削速度。而加工铝合金的面铣刀,由于其极高的切削速度,在大直径时转动惯量也会很大。因此,瓦尔特的加工铝合金的大直径铣刀采用了高强度铝合金刀体,极大地降低了转动惯量,增加了刀具的安全性。而今年瓦尔特也将推出能在尺寸调节过程中自动进行平衡适应的镗刀。
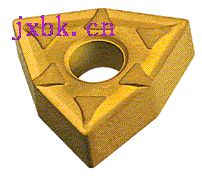 瓦尔特的Wiper车刀片
|
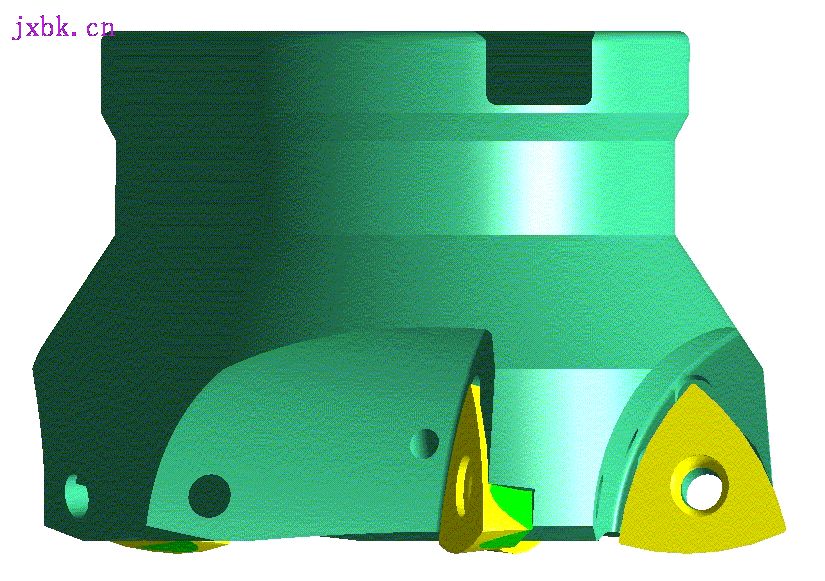 大进给铣刀 |
2. 提高进给速度
近年来,车加工中出现了一种被称为Wiper技术的新技术。所谓Wiper技术,就是用修光刃构成宽的精加工刀刃的技术。就技术原理而言,Wiper技术在铣削上的应用已经非常成熟。近年来,瓦尔特等刀具制造商将该技术移植到车削加工中,使车削的加工效率飞速提高,经济效益十分明显。笔者年前在上海一家中德合资汽车零部件制造公司进行过试验,根据工件的要求,允许的最大刀尖圆角为0.8mm,而表面粗糙度的要求为Ra0.4µm。按通常的方法,这样的加工进给率不能超过0.1mm/r(该客户实际采用的进给率为0.08mm/r)。小进给量的加工不但效率低,而且由于工件材料软而使断屑变得十分困难。在试验中我们使用了瓦尔特的Wiper车刀片来进行加工,进给量增加到0.3mm/r,结果不但加工表面的粗糙度达到要求,断屑问题得到了解决,而且加工效率提高到原来的375%。虽然刀具直接费用没有下降,但由于降低了切削时间,构成加工费用的重要组成部分机床费用也就得到大幅度的降低,从而降低了制造费用,用户也对此感到非常满意。
我们再来看一个铣刀大进给的范例。近年来,瓦尔特等刀具制造商开发了一种大进给的铣刀。这种铣刀将原先用于仿形加工的弧边三边形刀片用于平面加工,从而使这种铣刀具有非常小的主偏角(0°–15°)。小的主偏角带来径向力的减小,与立铣刀相比它的径向切削力减少至少约75%,使得工艺系统的抗振能力得到极大的加强,因此该刀具的最大进给已经达到每齿3.5mm,或者可以将刀具的悬伸加大到刀杆直径的8倍以适合深型腔加工的要求。
3. 增加切削深度
切削深度大的切削一般称为重切削。国际上原先只有少数几家刀具商制造使用立装刀片结构的重切削铣刀,但近年来包括瓦尔特在内的一些主要刀具商都已供应多种重切削铣刀。
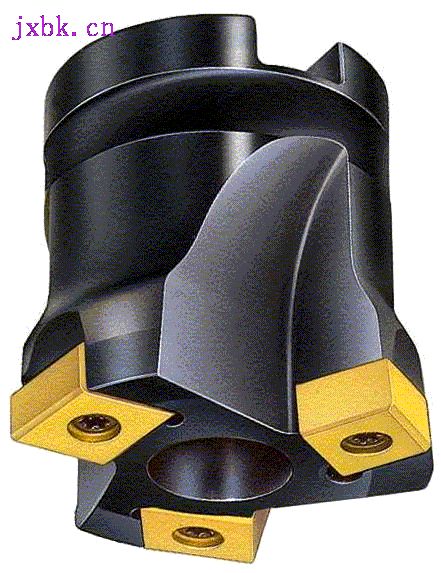 瓦尔特的插入式铣刀F2230 |
这里,我们介绍一种用于模具深腔粗加工的大余量切削铣刀。通常,我们在加工型腔时采用沿等高线切削的加工方法,即使采用爬坡法也属于斜向切削。这两种加工方法均有一定的径向切削力存在,在深腔加工中由于刀具悬伸较长,为了避免在径向切削力的周期性作用下产生振动,通常采用较低的切削用量,从而带来较低的切削效率。近年瓦尔特推出的插入式铣刀F2230,采用完全的轴向进给,从而在铣刀上几乎没有轴向切削力,切削用量和生产效率得以大幅度提高。2002年,我们在湖南一公司粗加工用30CrMnTi制造的传动轮,客户原先采用的是用国外著名刀具公司的玉米铣刀进行分层切削,由于整个粗加工时间长(耗时大约90分钟),在加工到一半时还需要更换刀片,而粗加工该工件的刀片消耗约300元人民币。现在采用瓦尔特F2230铣刀后加工效率大幅度提高,耗时减少到51分钟,一次装夹刀片后可以加工1.5-2个工件,粗加工该工件的刀片消耗降低至约100元人民币。由于刀具费用、机床费用、换刀费用都得到减少,他们由此降低年制造费用约9.8万元人民币。
多项技术的联合使用常常使切削效率得到极大的提高,从而对经济效益产生巨大的影响。在中国某柴油机制造企业,由于使用了瓦尔特新技术的老虎刀片,经济效益十分可观。
瓦尔特的老虎刀片(TigerTec)则是铸铁加工技术的一个飞跃。对于老虎刀片,瓦尔特的技术专家费了不少心思。他们一是改进了刀片基材以改善刀具的耐磨性,二是改进了氧化铝复合镀层与特殊中间层的连接结构以提高镀层的结合力,更令人拍案叫绝的是其首创的双色镀层技术。老虎刀片前刀面的增厚的黑色氧化铝能够有效地抵抗磨损,而后刀面的金色氮化钛则使我们能够有效地辨认刀具的磨损。
中国的一个著名柴油机制造企业原来使用一家著名的美国公司的产品。由于加工质量不理想,他们使用的线速度为165m/min,进给速度为341m/min(每齿进给为0.04mm),刀具寿命为30件。瓦尔特的老虎刀片将切削速度提高到了350 m/min,进给速度则达到2785m/min(每齿进给为0.18mm),是原来加工效率的817%,而刀具寿命也增加到117件。虽然瓦尔特老虎刀片的价格比他们原用的刀片贵了约43%,但他们全年用于该工序的刀片采购价格从原来的37,800欧元下降到8,289欧元,降低了74%的刀具费用。而机床成本则从原来的每30,000件50,773欧元下降到仅5,699欧元,下降幅度高达88.8%。综合其它因素,该柴油机制造商从提高加工效率中所得到的利益是降低了约83%的加工费用。
提高加工效率的另一个有效途径是采用复合加工,降低加工时间。在举世瞩目的世界第一条磁悬浮商业运行线的工程中,功能件的加工任务十分繁重。在该功能件上有一个上部带倒角的圆底槽,倒角和槽之间还有倒圆。客户客户原分3步加工,他们使用某国产特殊半径槽刀,刀片易崩刃。在这一工序上每天每台机床需要单价约5.00欧元的刀片80片,故每天每台机床的该刀片的费用约400欧元。然后再使用120o倒角刀具进行倒角,最后有3个工人专门从事手工进行R2倒圆,质量难以保证。瓦尔特向他们提供了一种特殊刀具,三个工序可以一次完成,而所有工序的加工每天每台机床消耗单价约15.00欧元的刀片8片,共计120欧元。因此,我们即使不计算客户原来倒角倒圆的加工费用,至少每天节约了280欧元的加工费用,并且质量得到了有效的保证。
提高加工效率不仅可以依靠刀具技术的进步,同时更应该重视合理选用刀具。在许多场合,加工效率很大程度上受工艺系统刚性的影响。众所周知,刀具工作时多数处于悬臂梁状态,它的刚性可以用以下公式近似计算:
f=
| F×l³
| =
| F×l³×64
|
|
|
3×E×I
| 3×E×d4×p | 式中:
F为径向力
l为悬伸长度
E为刀杆的弹性截面模量
d为刀杆直径
因此,我们提高工艺系统刚性主要应从这4方面考虑。即:
- 降低刀具的径向切削力,如采用类似F2330的小主偏角铣刀;
- 尽可能缩短刀具悬伸长度。在其他条件相同的情况下,如果悬伸比原来减少20%,进给或切深可增加将近100%。瓦尔特的螺纹连接式模块式铣刀(参见http://e-cuttech.com/WalterSrewFitPromotion.html),在制造诸如手机模具、工具(如扳手、可转位刀片等)模具时,常常由于减小了刀具的悬伸长度而大大增加刀具的刚性,从而使使用大切深或大进给切削而不产生振动提供了一种可能;
- 提高刀杆的弹性截面模量,如采用硬着合金或重金属刀杆;
- 增加刀杆直径。大直径的刀具通常刚性能得到极大提升,从而使加工成本被大大降低。
以上分析表明,提高加工效率是提高制造厂商经济效益的非常重要的途径。当然,对于其它降低制造成本的方法,虽然收效相对小些,我们还是应该尽一切可能来降低制造成本。
就刀具而言,降低制造费用的第二个有效途径就是延长刀具的使用寿命。
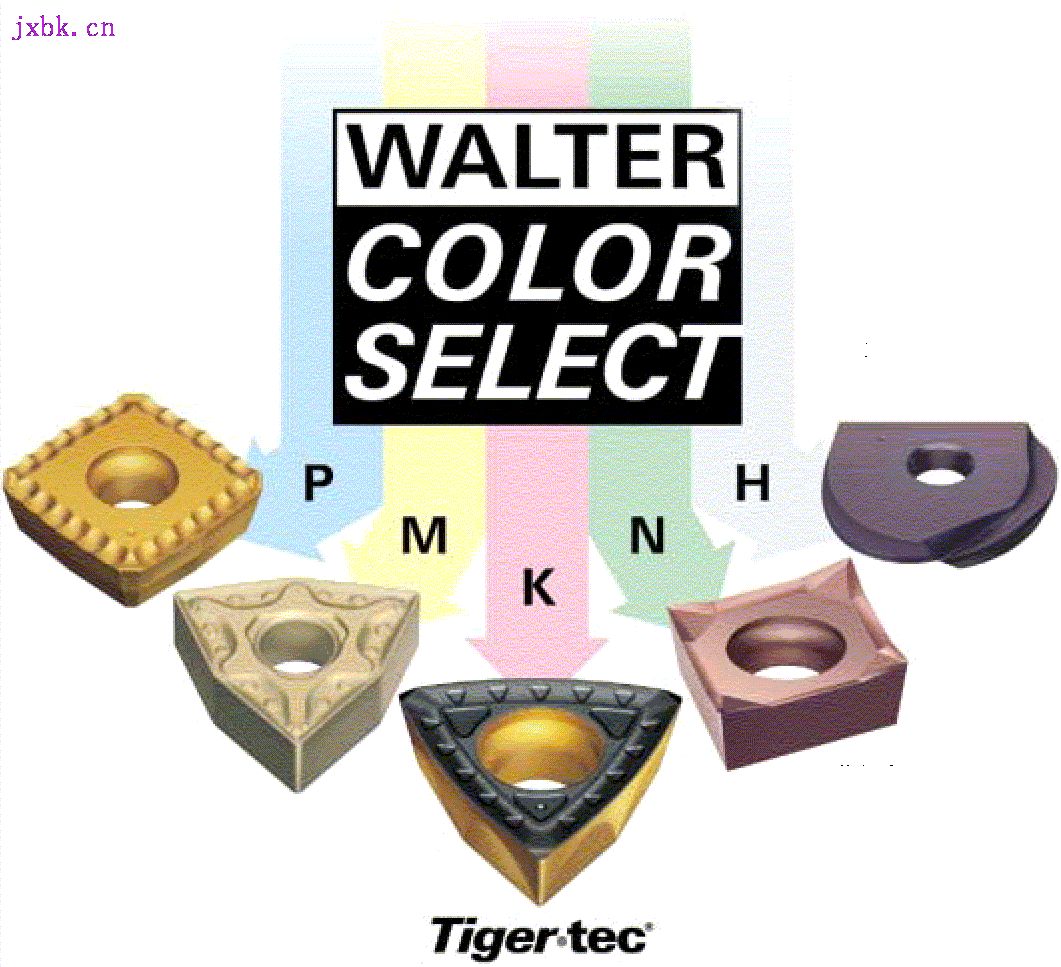 瓦尔特的颜色选择法 |
想得到理想的刀具寿命,首先应选择正确的刀具材料。瓦尔特在2002年首创并推出了直观的颜色选择法,使用户能在最短的时间内选择正确的刀片材质。如果用户需要加工钢件,他只要选择瓦尔特的金色刀片;如果用户需要加工不锈钢件,他只要选择瓦尔特香槟色刀片;如果用户需要加工铸铁,他只要选择黑金双色的老虎刀片;如果用户需要加工非铁金属材料,他只要选择紫铜色的刀片;而如果用户需要加工硬金属材料,他只要选择紫水晶色的刀片。
国外一个厂商在Okuma车削中心上加工硬度为28HRC不锈钢普通直轴连续切削,试用了许多刀具都不理想,最后采用了日本某著名企业的产品进行加工。在这之后我们向用户推荐了为加工不锈钢设计的香槟色刀片进行试验,结果让用户非常惊讶。因为瓦尔特的香槟色刀片的寿命竟然达到那家日本公司的两倍,而在这之前其他供应商的刀具寿命都远不能与这家日本公司相提并论。
韩国的一个汽车零部件制造商每年生产1,200,000件用灰口铸铁制造的刹车鼓,原先使用一家日本公司的车刀片进行加工。由于切削速度较高(200-376m/min),刀具寿命为每一刃口40件。瓦尔特的老虎刀片是专为铸铁加工而开发的刀片材质,在加工铸铁上的表现令人叹服。在那里,老虎刀片的寿命达到80件,从而使客户的年消耗值从20,625欧元下降到11,563欧元,降低刀具消耗44%。
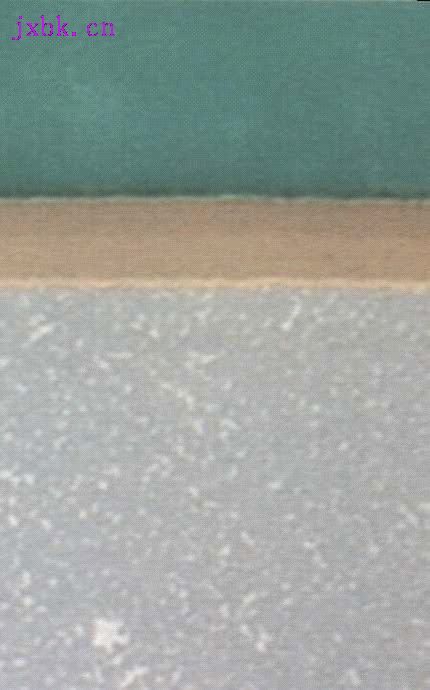 100层的WQM35
| 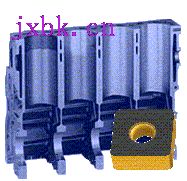 Mahle的汽缸体与老虎刀片
|
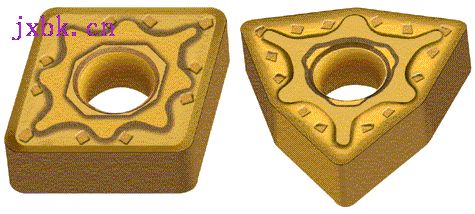 CN刀片(左)与WN刀片(右) |
在1999年的欧洲机床展览会上,瓦尔特推出了一类被命名为Quar?tec的刀片。其中有一种被命名为WQM 35的刀片采用精细的物理镀层的方法,将其刀片的镀层数增加到了100层。这种100层的镀层对于提高刀片的抗冲击能力发挥了巨大的作用。通常由于在高频的冲击作用下,镀层的表层会产生细微裂纹并迅速扩展造成膜层与基体的结合被破坏,刀具常常在正常寿命前就丧失了应有的切削能力。WQM 35的百层镀层使裂纹的扩展被有效地阻滞,刀具的寿命得到有效的延长。
想得到理想的刀具寿命,还需要合理使用刀具。比如在铣削时,由于交变热应力的作用,通常干加工能够取得比湿加工更长的刀具寿命;在模具铣削中,由于加工条件的稳定,横截面轮廓铣削的刀具寿命比纵截面轮廓铣削更长;球头铣刀的加工,由于避开切削速度为零的轴线,轴线倾斜的方式比轴线垂直的方式刀具寿命更长……
降低刀具采购费用也是降低制造成本的途径之一。从节约每一分钱的角度考虑,降低刀具的采购价格同样是制造业的一个选择。但降低刀具的采购价格绝不仅仅意味价格竞争。
德国著名的摩托车制造商Mahle进行了使用老虎刀片替代硅酸盐陶瓷刀片的试验。试验以前,Mahle的金属切削专家都表示用硬质合金来代替陶瓷刀片进行铸铁加工是难以想象的。因为陶瓷刀片容易达到600m/min的切削速度及0.5mm/r的进给量,这使得氮化硅陶瓷刀片在许多公司进行粗加工铸铁时成为首选。但通过试验,他们看到瓦尔特的老虎刀片不但完全达到了其原来使用的陶瓷刀片的技术水平和加工效率,而且减少了刀具破损的发生。在Mahle公司,老虎刀片主要用来加工发动机汽缸孔。由于老虎刀片属于硬质合金镀层刀片,其价格比陶瓷刀片也明显降低(虽然它比瓦尔特其它的硬质合金镀层刀片略高),从而给制造商带来十分明显的经济效益。在Mahle公司,由于采用老虎刀片代替陶瓷刀片,他们一年将降低刀具采购费用10,000欧元。
在最常见的普通内外圆车削中,目前的加工余量通常在3mm以下,而我们的制造业从业人员却有不少人或因刀具商从业人员的介绍和推荐不力,或因出于使用习惯,或由于对新技术了解不够,使用足以承受6mm以上加工任务的CNMG1204...的刀片。其实,不少刀具商(如瓦尔特)在几年以前就推出了WNMG0604...的刀片以在小余量加工的场合替代CNMG1204...。通常,由于两者的刀尖角完全相同,加工程序不需要作任何变动,在小余量加工的场合用W型刀片代替C型刀片一般不存在任何风险。同时,WNMG0604...不但价格比CNMG1204...要低一些,而且由于它比后者多50%的切削刃,经济效益非常明显。同样的利益也体现在用较小尺寸的刀片代替较大尺寸的刀片的情况,如在车削中用DN..07代替DN..11,在铣削中用SP..06或SP..09代替SP..12等等。这样的改变并不复杂,经济效益却可能不容小窥。
因此,我认为,刀具商作为供应链的一个组成部分,与制造商共同努力降低制造成本是责无旁贷的任务。优选刀具、优化刀具材料和几何参数、合理使用刀具、强化刀具管理等都是降低制造成本的有效途径。瓦尔特作为制造业的系统合作伙伴,1999年欧洲机床展览会上推出的Quar®tec使加工效率提高了50%,2001年欧洲机床展览会上推出的Tiger®tec使加工效率提高了75%,而今年在欧洲机床展览会上将推出有望使加工效率提高一倍的新型刀具。尽管如此,我认为最重要的并不仅是销售刀具本身,而是我们的客户是否选择了正确的刀具,是否用好了我们的刀具,是否由于使用我们的刀具而提高了市场竞争能力。作为一个负责任的刀具商,应该在努力降低自身刀具制造成本来降低用户刀具采购成本的同时,保留合理的利润空间来保证对新技术、新产品研发的投入力度,从而使我们的客户能够不断地享受刀具业的新技术,实现制造成本的不断降低和市场竞争能力的不断提高。过度降低价格的恶意竞争不仅是损害自身的发展空间,从长远来说也是损害包括汽车制造业在内的整个制造业的长远利益。我本人衷心希望大家都能从供应链的整体利益出发,在维护自身生存发展空间的同时,关心供应链中其他伙伴的生存发展空间,真正实现双赢甚至多赢的战略目标,走上共同发展的阳关大道。 |
|
我有问题,我要进入论坛 |
出处:本站原创 作者:佚名 | |
|